Table of Contents
When it comes to welding, the first thing that comes to mind may be the connection of metal parts. So how are various plastic products seen in daily life welded? Next, the laser welding machine manufacturer-BuyCNC will popularize plastic welding from the aspects of plastic welding process method, plastic laser welding machine process, plastic laser welding industry application and development trend.
Can all plastic materials be welded?
Can any plastic material be welded? Plastics are classified according to their physical and chemical properties into thermosets and thermoplastics.
Among them, thermosetting plastics are chemical molecular structures, which are generally formed at one time. The switch panel and the bowl for children are all processed from thermosetting plastics. They have the characteristics of high temperature resistance, hard texture and difficult to melt. They will not soften after heating, and will be directly decomposed by excessive heating.
Another type of thermoplastic is markedly different in that they soften or melt when heated, flow formable, and can be reheated many times over. It follows from this that not all plastic materials can be welded.

What are the types of plastic welding processes?
There are four main types of commonly used plastic welding process methods:
(1) Hot plate welding – welding after the heating of the hot plate, after the product is melted, the hot plate is taken out, and the product is pressurized to achieve welding;
(2) Ultrasonic welding – using high-frequency vibration waves to transmit to the surface of the object to be welded, under pressure, frictional heat is generated to weld the product;
(3) Laser welding – Laser welding technology is a technology that uses the heat generated by a laser beam to melt the plastic contact surface, thereby bonding thermoplastic sheets, films or molded parts together.
(4) Vibration friction welding – two plastic parts contact and rub against each other under a certain pressure, amplitude and frequency. Heat generated by friction causes the material to melt at the weld interface. Under pressure, molten plastic flows out of the weld area to form flash. After the vibration ceases, the molten plastic layer solidifies and produces a strong joint;
Among the advantages and disadvantages of these four welding methods, the advantages of plastic laser welding are particularly obvious. It can process complex parts, and has the characteristics of short welding cycle, online monitoring and low equipment maintenance cost.
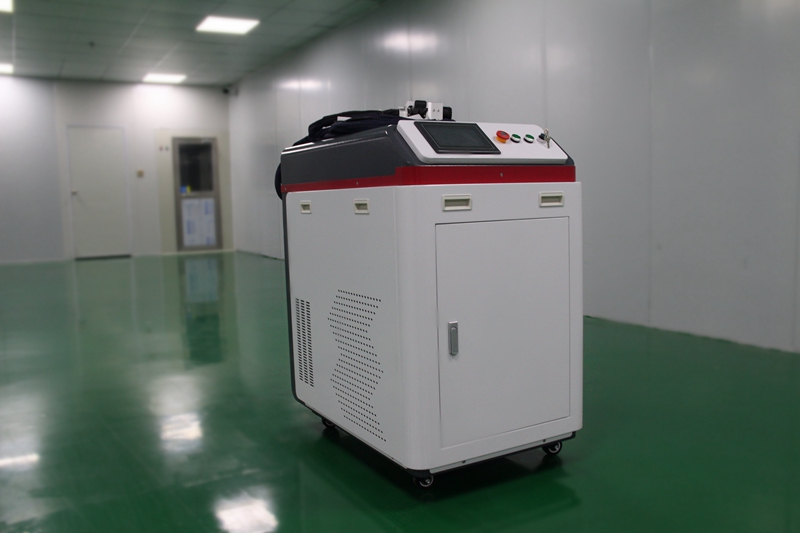
Principle of plastic laser welding
The laser plastic welding method requires that the upper and lower layers of the material to be welded have good permeability and good absorption respectively for a certain wavelength of laser light. Based on this, plastic laser welding is also called laser transmission welding.
During welding, the laser penetrates the upper layer material and is absorbed by the lower layer material at the joint surface of the upper layer material and the lower layer material and generates heat, and the heat is transferred between the upper and lower layer materials to melt the joint surface. Under the action of the pressure and thermal expansion of the fixture, they diffuse and entangle with each other, and the van der Waals force is generated to realize the welding.
Since the plastic welding process requires pressure, the welding of plastic parts has corresponding requirements for its structure. The welding of plastic parts is generally an upper and lower lap structure. For pipe parts, the pipe welding with interference fit can be realized.
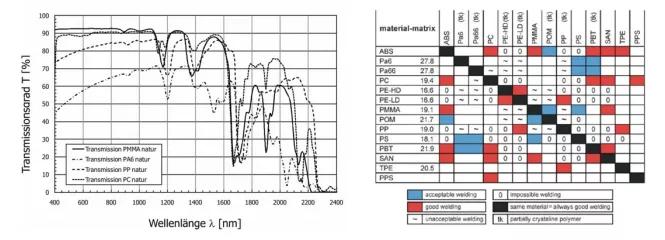
Types of plastic welding methods
Plastic welding methods are generally divided into four categories:
(1) Contour welding: The laser moves along the contour of the plastic welding layer and melts it, gradually bonding the plastics together. Mainly used for welding parts with regular shape and welding speed requirements;
(2) Scanning welding: Also known as quasi-synchronous welding, it combines the above two welding technologies. The high-speed laser beam is generated by the optical device and moves along the part to be welded, so that the whole welding part gradually heats up and fuses together. This method has higher requirements for laser emission equipment;
(3) Simultaneous welding: use a laser transmitter with multiple laser ports to adjust the direction and shape of the laser beam through optical devices; the laser beam is guided by the program and welds along the contour of the welding layer to melt the entire contour at the same time and glued together. Mainly used for parts with large welding contact area and high welding consistency requirements;
(4) Mask welding: The laser beam in the invalid area is blocked by the pre-made template, only the precise welding part is exposed, and only the welding area is melted to realize the welding process. This welding technology has high precision and is currently the most widely used laser welding technology. It has strong equipment versatility, simple template fabrication and low cost, and can achieve high-precision welding as low as 10 μm.
Laser Welding Machine For Sale

In fact, not only Zhang Feng, but also Bai Xuan and Zhang Ji are very can reducing caffeine lower blood pressure familiar priligy dapoxetine amazon
Your comment is awaiting moderation.