Table of Contents
Principle of Laser Steel Welding Machine
The steel welding machine is the most popular welding machine nowadays. This laser welding machine has been used in various fields, so do you know what the principle of laser welding machine is? Laser welding aluminum machine is to radiate a high-intensity laser beam to the metal surface, and through the interaction of the laser and the metal, the metal is melted to form welding. In the process of laser-metal interaction, metal melting is only one of the physical phenomena.
Sometimes time energy is not mainly converted into metal melting, but manifested in other forms, such as vaporization and plasma formation. However, to achieve good fusion welding, metal melting must be the main form of energy conversion. For this reason, it is necessary to understand the various physical phenomena produced by the interaction between laser and metal and the relationship between these physical phenomena and laser parameters. By controlling the laser parameters, most of the laser energy can be converted into metal melting energy to achieve welding. Purpose.
This is why the laser welding machine is so warmly welcomed. This welding machine is more efficient than the original ordinary welding machine and can weld all materials better.
Process Parameters Of Laser Steel Welding Machine
Compared with other welding machines, the process parameters of laser welding aluminum machine are very high. The laser welding machine performs very well in terms of power density, laser pulse waveform, laser pulse width, and defocus. .
1. Power density
Power density is one of the most critical parameters in the processing of a stainless steel welding machine. With a higher power density, the surface layer can be heated to the boiling point within a microsecond time range, resulting in a large amount of vaporization. Therefore, high power density is beneficial for material removal processing, such as punching, cutting, and engraving. For lower power density, it takes several milliseconds for the surface temperature to reach the boiling point. Before the surface layer vaporizes, the bottom layer reaches the melting point, which is easy to form a good fusion weld. Therefore, in conductive laser welding, the power density is in the range of 104~106W/cm2.
2. Laser pulse waveform
The laser pulse waveform is an important issue in the work of a steel welding machine, especially for sheet welding. When a high-intensity laser beam hits the surface of the material, 60~98% of the laser energy will be reflected and lost on the metal surface, and the reflectivity changes with the surface temperature. During a laser pulse, the reflectivity of the metal changes greatly.
3. Laser pulse width
Pulse width is one of the important parameters of laser welding aluminum machine. It is not only an important parameter different from material removal and material melting, but also a key parameter that determines the cost and volume of processing equipment.
4. The influence of defocusing amount on welding quality
The laser stainless steel welding machine usually needs a certain amount of defocus, because the power density in the center of the spot at the laser focal point is too high, and it is easy to evaporate into a hole. On each plane away from the laser focus, the power density distribution is relatively uniform.
There are two defocusing methods: positive defocus and negative defocus. If the focal plane is above the workpiece, it is a positive defocus, otherwise it is a negative defocus. According to geometrical optics theory, when the positive and negative disjunctions are equal, the power density on the corresponding plane is approximately the same, but in fact the shape of the molten pool obtained is different.
When the defocus is negative, a greater penetration depth can be obtained, which is related to the formation process of the molten pool. Experiments have shown that the laser heating 50~200us of the material begins to melt, forming liquid metal and vaporizing, forming city pressure steam, and spraying at a very high speed, emitting dazzling white light.
At the same time, the high concentration of vapor causes the liquid metal to move to the edge of the molten pool, forming a depression in the center of the molten pool. When the defocus is negative, the internal power density of the material is higher than that of the surface, and it is easy to form stronger melting and vaporization, so that the light energy can be transmitted to the deeper part of the material. Therefore, in practical applications, when the penetration depth is required to be large, the negative defocus is used; when the thin material is welded, the positive defocus should be used.
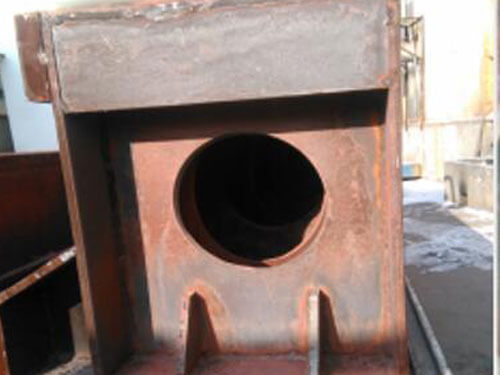
Laser Welding Aluminum Machine Process Method
As the most popular welding machine, the laser welding aluminum machine can weld many kinds of materials, and can weld many different materials, whether it is metal sheet or wire, or different metals. Our steel welding machine can be welded.
1. Welding between slices: Including four process methods: butt welding, end welding, center penetration fusion welding, center perforation fusion welding.
2. Wire and wire welding: Including wire-to-wire butt welding, cross welding, parallel lap welding, T-shaped welding and other 4 process methods.
3. Welding of metal wires and block components: Laser welding can successfully realize the connection between the metal wire and the block element, and the size of the block element can be arbitrary. Attention should be paid to the geometric dimensions of the wire-like components during welding.
4. Welding of different metals: Welding different types of metals must solve the weldability and the range of weldable parameters. Laser welding between different materials is only possible with certain material combinations.
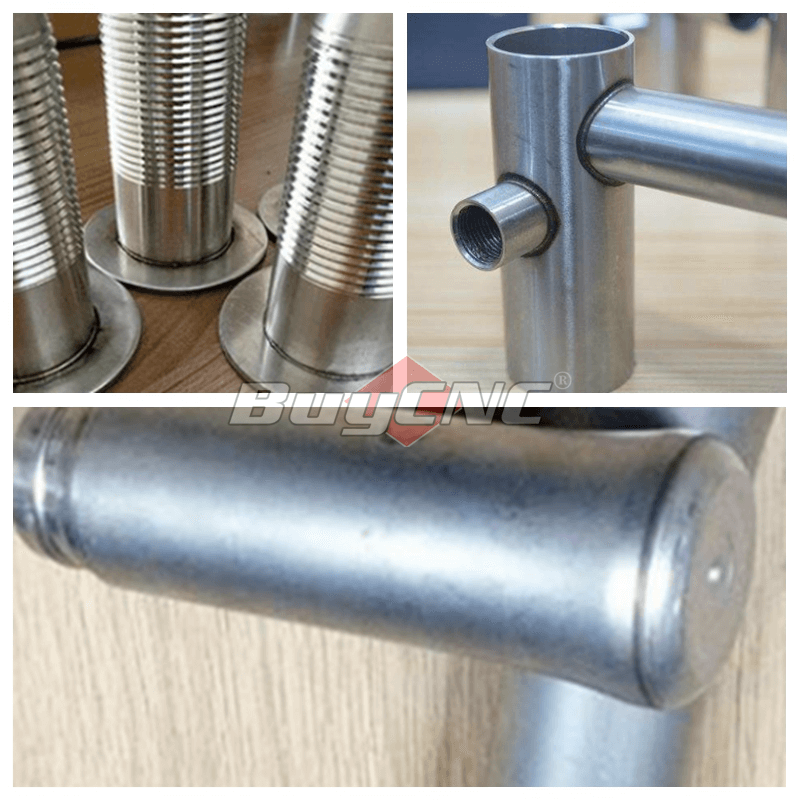
Advantages Of Laser Stainless Steel Welding Machine
Compared with other welding technologies, the laser welding aluminum machine has many advantages, so the main advantages of laser welding aluminum machine are:
1. Fast speed, large depth and small deformation.
2. It can be welded at room temperature or under special conditions, laser stainless steel welding machine is simple. For example, when the laser passes through an electromagnetic field, the beam will not shift; the laser can be welded in vacuum, air and certain gas environments, and can be welded through glass or materials that are transparent to the beam.
3. It can weld refractory materials such as titanium, quartz, etc., and can weld heterogeneous materials with good results.
4. After the laser is focused, the power density is high. When welding high-power devices, the aspect ratio can reach 5:1, up to 10:1.
5. Micro welding is possible. After the laser beam is focused, a small spot can be obtained, and it can be accurately positioned, which can be applied to the assembly welding of micro and small workpieces that are mass-produced automatically.
6. It can weld hard-to-access parts, and implement non-contact long-distance welding, which has great flexibility. Especially in recent years, the use of optical fiber transmission technology in YAG laser processing technology has made laser welding technology more widely promoted and applied.
7. The laser beam is easy to realize the beam splitting according to time and space, and can carry out multi-beam simultaneous processing and multi-station processing, which provides conditions for more precise welding.
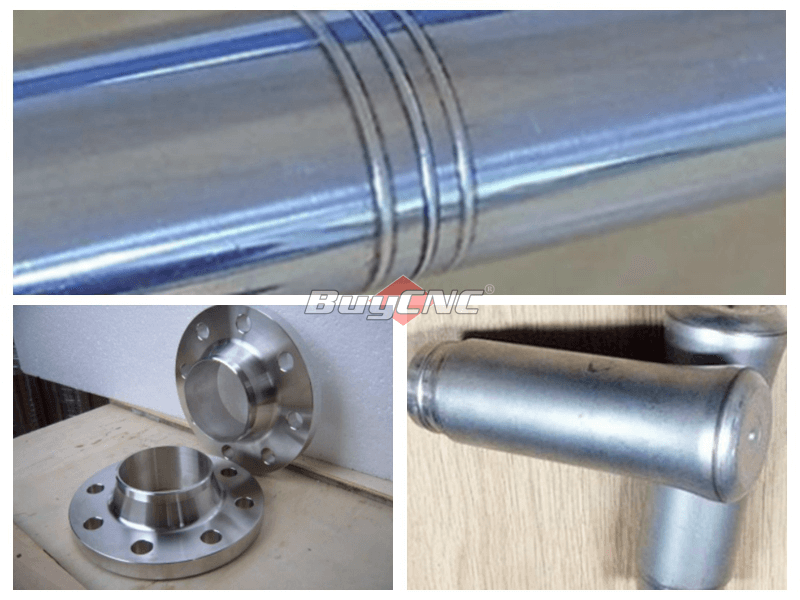
Disdavantages Of Laser Steel Welding Machine
However, laser welding also has certain limitations:
1. The laser welding aluminum machine requires high precision in the assembly of weldments, and requires that the position of the beam on the workpiece cannot be significantly shifted. This is because after the laser is focused, the spot size is small and the weld is narrow, which is filled with metal materials. If the assembly accuracy of the workpiece or the positioning accuracy of the beam does not meet the requirements, it is easy to cause welding defects.
2. When the laser welding aluminum machine is working, the maximum weldable thickness of the laser welding machine will be limited to a certain extent. If you want to weld a workpiece with a thickness far greater than 19mm, then it is not suitable for welding with a steel welding machine.
One is that the position of the weldment must be very precise and must be within the focus range of the laser beam; the second is that when the weldment needs to use a fixture, it must be ensured that the final position of the weldment must be aligned with the welding point that the laser beam will impact; the third is the maximum possible The welding thickness is limited, and the workpiece with a penetration thickness far more than 19mm is not suitable for laser welding on the production line.
3. The cost of the laser welding aluminum machine and its related systems is relatively high. Compared with the ordinary welding machine, the one-time investment of the laser welding machine is relatively large.
Laser Steel Welding Machine For Sale
