Table of Contents
What is the Best Aluminum Welder Machine
The Best aluminum welder is one of the laser welding machines. It is a laser welding machine that works for aluminum or aluminum alloy. Aluminum alloy is a non-ferrous metal material. It has light weight and good toughness. , High strength and other advantages, widely used in aerospace, automotive, machinery manufacturing and chemical industries, the portable aluminum welder machine can increase its processing speed and greatly reduce heat input, thereby increasing production efficiency and improving welding quality. Compared with other laser welding machines, it has different advantages and advantages and is welcomed and loved by various machinery manufacturers.
Feature And Advantages of Best Aluminum Welder
The aluminum and aluminum alloy processed by the best aluminum welder machine have the characteristics of low density, relatively high strength, good wear resistance, electrical conductivity, thermal conductivity, and good mechanical properties at low temperatures. It is widely used in aviation Industries such as aerospace, automobile, electrical engineering, chemical industry, transportation, national defense and so on. The chemical activity of aluminum and its alloys is very strong, and it is easy to form a refractory oxide film on the surface. In addition, aluminum and its alloys have strong thermal conductivity, which is easy to cause non-fusion phenomenon during welding. Since the density of oxide film is close to that of aluminum alloy, it is easy to become inclusions of weld metal. Compared with argon tungsten arc welding or melting argon arc welding, laser welding of aluminum alloy has a fast speed, a narrow welding seam, a small thermal strain, and a reduced overlap joint, which can greatly reduce the weight. Therefore, many scientists began to explore the possibility of laser welding aluminum alloys.
The processed aluminum and aluminum alloy have good cold and hot workability and weldability, and can be welded by conventional fusion welding methods. The conventional welding method is argon arc welding. Plasma arc welding, resistance welding and electron beam welding, etc. Cold pressure welding can also be used. Ultrasonic welding. Brazing, etc. The heat power is large. The welding method with good energy concentration and protection effect is more suitable for the welding of aluminum alloy. Gas welding and arc welding are easily replaced by argon arc welding in aluminum alloy welding, and are only used to repair and weld unimportant welding structures. Aluminum and aluminum alloy welding wires are divided into two categories: homogeneous materials and dissimilar materials. In order to obtain a welded joint with good performance, the welding wire suitable for the base metal should be selected as the filler material according to the use requirements of the welded component.
Compared with other traditional welding, the laser welding of the portable aluminum welding machine has the main advantages of fast speed, large depth, and small deformation. It can weld refractory materials such as titanium, quartz, etc., and can apply Welding, the effect is good. At the same time, the small aluminum welder machine also has certain limitations, requiring the precision of welding equipment, and the position of the beam on the workpiece can be significantly shifted. The cost of the laser and its phase relationship system is relatively high, and the one-time investment is relatively large. So the following are the specific advantages of small aluminum welder machine.
Advantage of best aluminum welder
1. High energy density, low heat input, small thermal deformation, narrow melting zone and heat-affected zone, and large penetration depth;
2. The high cooling rate results in a fine weld structure and good joint performance;
3. Compared with contact welding, laser welding does not use electrodes, so it reduces man-hours and costs;
4. The vacuum atmosphere of electron beam welding is not required, and the shielding gas and pressure can be selected. The shape of the welded workpiece is not affected by electromagnetics and does not produce X-rays;
5. It can weld metal materials inside closed transparent objects;
6. The laser can be transmitted over a long distance with optical fiber, so that the process is adaptable. With the computer and manipulator, it can realize the automation and precise control of the welding process.
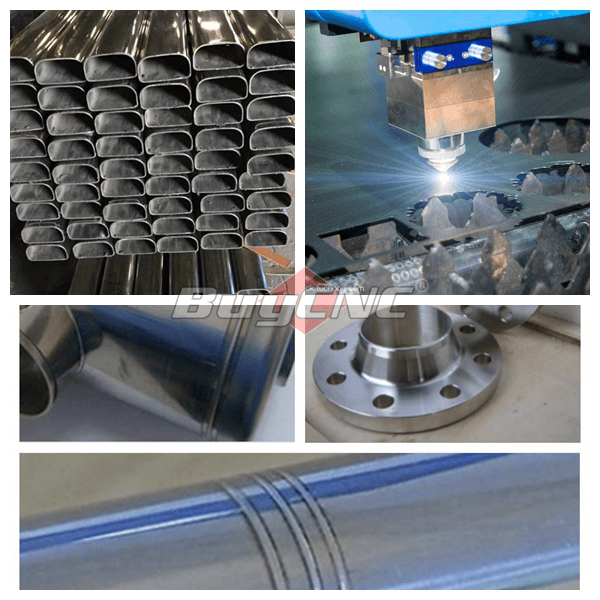
The difficulties of the small aluminum welder machine
The first point: the surface of aluminum alloy is prone to produce a refractory oxide film, which requires the use of a high-power density welding process;
The second point: the thermal conductivity of aluminum alloy is large (about 4 times that of steel). At the same welding speed, the heat input is 2 to 4 times larger than that of welded steel. Therefore, the welding of aluminum alloy requires the use of high-efficiency welding methods with high energy density, low welding heat input, and high welding speed.
The third point: extremely easy to oxidize. In the air, aluminum is easily combined with oxidation to form a dense aluminum oxide film with a high melting point, far exceeding the melting point of aluminum and aluminum alloys. The density of aluminum oxide is 3.95-4.10g/cm3, which is about 1.4 times that of aluminum. The surface of aluminum oxide film is easy to absorb moisture. When welding, it hinders the fusion of basic metals, and it is easy to form pores, slag, and Defects such as lack of fusion, causing degradation of weld performance.
The fourth point: easy to produce pores. The main cause of pores in aluminum and aluminum alloy welding is hydrogen. Since liquid aluminum can dissolve a large amount of hydrogen, while solid aluminum hardly dissolves hydrogen, when the temperature of the molten pool is rapidly cooled and solidified, hydrogen is too late to escape and is easy to be welded. Gathered in the slit to form pores. Hydrogen holes are difficult to completely avoid. There are many sources of hydrogen, such as hydrogen in the arc welding atmosphere, and the oxide film on the surface of the aluminum plate and the welding wire adsorbs moisture in the air.
Fifth point: The welding seam has a large tendency to deform and form cracks. The linear expansion coefficient and crystalline shrinkage of aluminum are about twice as large as steel, which is prone to large internal stress of welding deformation, which will promote the generation of thermal cracks on the rigid structure.
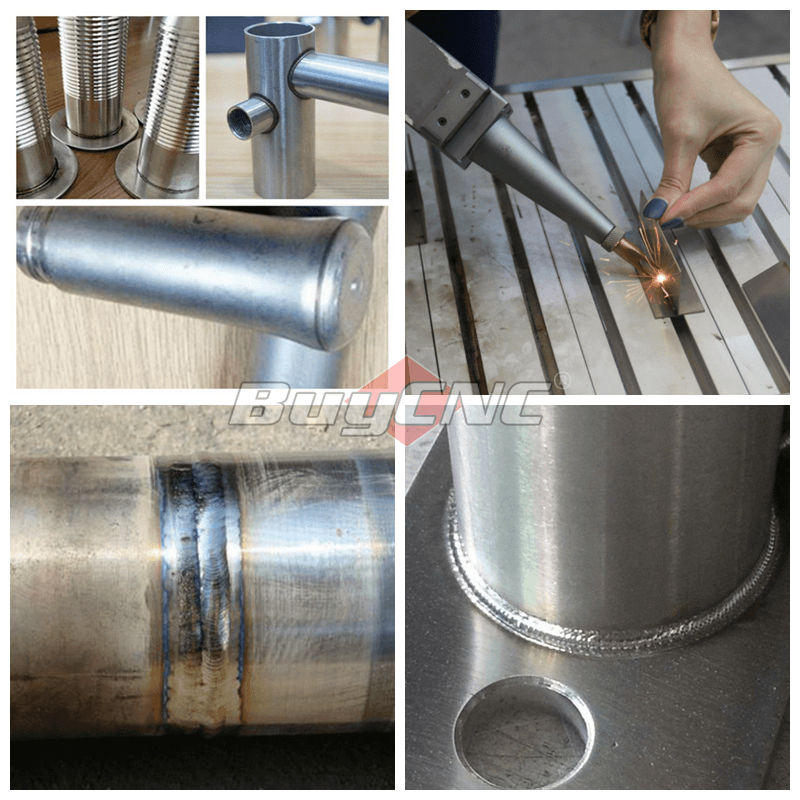
The ways to solve the welding difficulties of the best aluminum welder
1. Set up gas protection device
The factor that has the greatest influence on the loss of low melting point elements in aluminum alloy is the pressure when the gas is sprayed from the nozzle. By reducing the nozzle diameter, increasing the gas pressure and flow rate can reduce the burning loss of Mg, Zn, etc. during the welding process, and it can also Increase penetration. There are two blowing methods, direct blowing and side blowing. You can also blow up and down the weldment at the same time. The blowing method can be selected according to the actual situation during welding.
2. Perform surface pretreatment
Aluminum alloy has a high reaction to laser. Proper surface pretreatment of aluminum alloy, such as anodic oxidation, electrolytic polishing, sandblasting, sandblasting, etc., can significantly increase the absorption of beam energy on the surface. Studies have shown that the tendency of aluminum alloys to crystallize cracks after the oxide film is removed is greater than that of the original aluminum alloys. In order not to damage the surface state of the aluminum alloy, but also to simplify the laser welding engineering process, the pre-welding method can be used to increase the surface temperature of the workpiece to increase the material’s absorption rate of the laser.
3. Introduce alloying elements
Preventing the occurrence of hot cracks in aluminum alloy is one of the key technologies of aluminum alloy laser welding machine. 6000 series alloys have strong crack sensitivity. When ω(Mg2Si) =1%, hot cracks will appear. Adjust the chemical composition of the molten pool to improve it by adding suitable alloying elements, such as adding Al-Si or Al-Mg -Si powder has certain advantages in reducing cracks. In addition, wire feeding can be used to improve the welding effect and obtain a uniform weld. The hardness of the weld is also increased. The content of Mg and Si in the dendrite in the fusion zone increases due to the increase in the concentration of the filler material. Increase the strength of the joint. Usually 6063 and 6082 aluminum alloys are filled with Al-5Si and Al-7Si welding wires, 6013 and 6056 plates are welded with CO2 and Nd: YAG lasers, respectively, and Al-12Si welding wires are filled.
The Development Prospects of the Best Aluminum Welder
Nowadays, aluminum alloy products are not uncommon. Aluminum alloy doors and windows, pots and pans, etc. are all made of aluminum. The ordinary use of aluminum alloy has also promoted the development of aluminum alloy continuous welding technology, which is equivalent to laser welding machine technology and has entered the market area of aluminum application. Aluminum workpieces are generally completed by splicing, screwing, welding and other processes. Due to man-made reasons, the splicing place is often deformed to cause the aluminum plate to fall off, warp, etc., and the service life is greatly reduced; if the screw is used, the customer is unwilling to use it because of the hand feeling;
As for welding, in the past production practice, the welding of aluminum products commonly used tungsten argon arc welding and melting argon arc welding, although these two welding methods have high energy density, welding aluminum alloy can achieve good joints, but There are still shortcomings such as poor penetration, large welding distortion, and low production efficiency. Using these traditional welding methods applied to ferrous metals to weld aluminum alloys cannot meet the industrial requirements of high efficiency, flawlessness and good performance.
There are a lot of difficulties in these traditional aluminum alloy welding processes. Aluminum alloys have poor heat resistance. Generally, aluminum alloys are not resistant to high temperatures, have large expansion coefficients, and are prone to welding deformation and welding cracks. Because of these welding difficulties, it makes manufacturers worry day and night that they can’t find a better welding method. These inconspicuous omissions often bring unexpected troubles, and the use of best aluminum welder can easily solve these small problems. The flaws, which effectively guarantee the integrity of the processed parts and are not damaged, and improve the processing quality of the workpieces.
The best aluminum welder is because the laser beam is realized by pulsed or continuous laser beam, aluminum laser welding machine has high energy density, low heat input, small thermal deformation, narrow melting zone and heat-affected zone, large penetration depth, and high cooling rate The fine weld structure is obtained, and the joint performance is good, and it can weld the metal material inside the closed transparent object. Compared with the traditional contact welding, the best aluminum welder does not use the electrode, which reduces the man-hour and cost and improves the processing efficiency of the factory. Therefore, the best aluminum welder has a good development prospect.
Laser Aluminum Welding Machine For Sale
