The air compressor is an indispensable accessory in the laser cutting machine. Do you know anything about it? Do you know the function of the air compressor? Next, we will introduce the specific function of the air compressor to you. First of all, before introducing the air compressor, let’s introduce the laser cutting machine. With the rapid development of science and technology, more and more people begin to use laser cutting machines to process metal materials. The basic principle of laser cutting machine work: the workpiece is irradiated with a focused high-power and high-density laser beam, and the irradiated material rapidly melts, vaporizes, ablates or reaches the ignition point. material, so as to realize the cutting of the workpiece. Laser cutting is a typical thermal cutting method. In fact, it is simple to understand. It is similar to the traditional cutting saw, which is a bottle of acetylene and a bottle of oxygen. It’s just that laser cutting can achieve higher temperatures, higher precision, and higher efficiency.
Why do fiber laser cutting machines need air compressors?
The fiber laser cutting machine is assembled from many parts, but there are many parts that you don’t know what their functions are, and the air compressor is one of them. Many people think that the existence value of the air compressor is very low, can it be removed to save costs? In fact, this is a very wrong idea. Every component has its own value and reason. So what exactly is a fiber laser cutting machine air compressor? what’s the function? See the content below to understand.
What is the fiber laser cutting machine air compressor?
In fact, air compressors are often screw air compressors, and screw compressors are rotary positive displacement compressors, in which two rotors with helical gears mesh with each other, so that the volume of the meshing place between the two rotors changes from large to small, thereby The gas is compressed and discharged. So why should every fiber laser cutting machine have this thing? Is this thing a must have? Next, BuyCNC will introduce the specific function of the air compressor to you.
What is the function of the air compressor of the fiber laser cutting machine?
Fiber laser cutting machines must use protective gas when working, and air is of course the simplest and most economical protective gas. So an air compressor is essential for every fiber laser cutting machine. Compressed air is an integral part of the air supply system of the laser cutting machine, and high-quality compressed air guarantees the stable use of the laser cutting machine. Fiber laser cutting machine can meet the cutting requirements of various materials and complex shapes. However, its operation is inseparable from clean, dry and stable compressed air. A part of the compressed air, high-purity oxygen and high-purity nitrogen constitutes the cutting gas and is supplied to the cutting head. Part of it is used as a power source to supply the cylinder of the clamping table, and the last part is used to purge and dedust the optical path system. The compressed air discharged from the air enters the air control cabinet through the air storage tank and the dryer, and then passes through a set of sophisticated processing systems to become clean and dry air, which is finally divided into three paths, which are used as cutting gas, cylinder power gas source and The positive pressure dedusting gas in the optical path maintains the normal operation of the fiber laser cutting machine.
The above is the main content of the fiber laser cutting machine air compressor. The existence of every part is the key to the smooth operation of the fiber laser cutting machine, so it is wrong to think that some parts are unimportant.
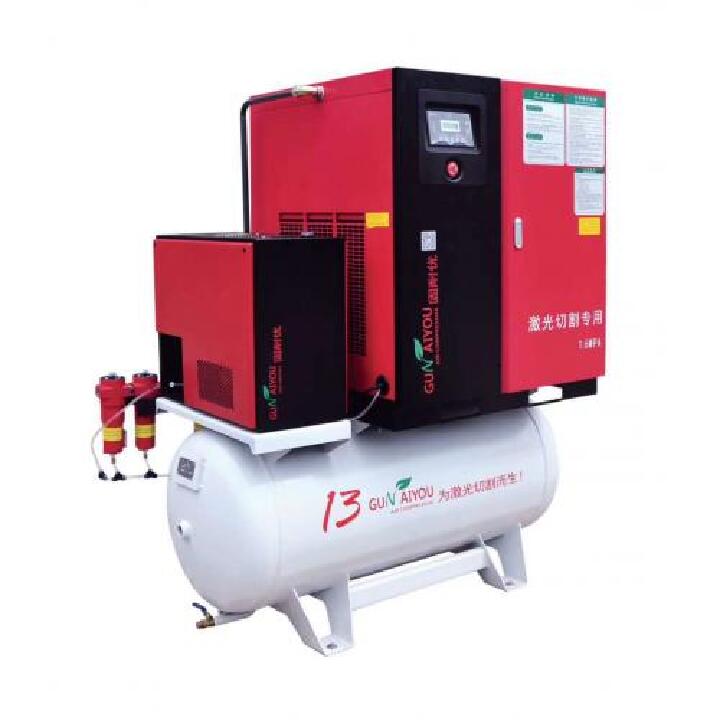
How to use the air compressor better for the light cutting machine?
First of all, when the fiber laser cutting machine uses the laser to cut the workpiece, the quality of the compressed air, the quality of the workpiece material, and the performance and quality of the laser cutting equipment all affect the cutting accuracy and surface quality. If the quality of the material used for processing the workpiece is poor, and there are defects such as cracks, sand inclusions, and pores, it will greatly increase the reject rate of the final molded parts. stability has an impact.
The impact of air compressor failure on fiber laser cutting machine equipment
(1) Insufficient outlet pressure: the cutting effect of the equipment is poor, the cylinder of the equipment cannot be opened normally, and the worktable cannot be exchanged normally.
(2) High oil and water content in the gas outlet: pollution of the auxiliary gas circuit, pollution of the proportional valve, pollution of the cutting head lens, and ultimately poor cutting effect.
Precautions for the use of air compressors:
(1) Manually exhaust and drain the air tank before starting the machine every day;
(2) 3 minutes after turning on the refrigeration dryer → turn on the compressor until the pressure in the pipeline is greater than 0.5MPa → turn on the adsorption dryer;
(3) When shutting down, it is necessary to ensure that the pipeline pressure is greater than 0.5MPa before closing the adsorption test dryer;
(4) Note that the compressor fan starts and stops normally and the temperature is normal;
(5) Please maintain the air compressor regularly in strict accordance with the air compressor maintenance regulations.
The use of compressed air for laser cutting machines
There are three uses for cutting gas, cylinder power gas source and optical path positive pressure dust removal.
Among them, cutting gas is the main gas, accounting for about 80~90% of the total gas demand. If the auxiliary gas source is oxygen or nitrogen, compressed air is also required for the other two purposes, but the flow rate is very small, and ordinary power can be used with compressed air.
Compressed air, as an auxiliary gas for laser cutting, mainly has three aspects: pressure, flow rate and air source quality.
pressure
When the laser power is large enough, the higher the pressure, the better the cutting quality and the higher the cutting efficiency.
But if the laser power is not strong enough, no amount of pressure will help. After all, the laser power is high enough to melt the cut material faster.
However, in the current market, the pressure of the air compressor supporting the laser cutting machine continues to rise, from 8 kg to 13 kg in the early stage, to 15 kg, and is currently developing to 20 kg.
At the same time, the price of high-power laser cutting machines is also falling. Therefore, when purchasing the pressure of an air compressor, it is recommended that users try to prefer higher than lower. It is better to choose the one with higher pressure, so as to be compatible with the later cutting machine with higher power.
flow
The size of the flow mainly depends on the size of the nozzle. As mentioned earlier, the nozzle accounts for 80~90% of the gas consumption. The nozzle of the laser cutting machine has many specifications, and there are 7 common specifications: 1.0, 1.5, 2.0, 2.5, 3.0, 3.5, 4.0.
The determination of this flow rate can be obtained by calculating the nozzle flow rate, or querying through the nozzle flow meter, or directly asking the laser cutting machine manufacturer.
quality of compressed air
The quality of compressed air has a very direct impact on the quality of laser cutting.
The compressed air contains water mist and oil. If it is not cleaned, high pressure is sprayed on the protective mirror surface of the laser cutting head, which will seriously affect the transmission of the laser beam, disperse the focus, and cause the product to be cut through and produce waste. Ultra-high-power laser cutting machines may also burn out the laser head.
Therefore, the compressed air system supporting the laser cutting machine is extremely sensitive to the content of oil and water, requiring no oil, no water and no dust. In fact, the biggest difficulty in the compressed air system of the laser cutting machine is the drying and purification device of the compressed air.
Oil-free products can be used to remove oil in principle, such as oil-free pistons, oil-free scrolls, oil-free screws or micro-oil screw machines to remove oil through multi-stage filtration.
The removal of water requires a dryer, and the performance of the dryer must be excellent.
For dust removal, it is necessary to configure a high-precision filter group with sufficient accuracy to fully filter out oil and dust particles.
Compressed air after treatment:
The pressure dew point needs to reach 2~5℃
Residual oil content≤0.001 ppm
Particulate matter content≤0.01 μm
Currently in the industry, it is a special product launched for laser cutting machines. Usually the micro-oil screw and post-processing equipment are skid-mounted together to form a complete air source system.
This kind of air compressor is usually more scientific, more reliable, and more secure than users who purchase a single product for configuration, or hand over to middlemen for configuration.