The best way Of How to cut metal
Why we choose metal cut and How to cut metal
Now the metal cutting industry has been widely used in the field of daily life. As people use more and more metals, the current metal cutting suppliers can no longer fully meet the increasing needs of people, so the metal cutting industry is now able to obtain rich interest in the society. So do you want to know how to use a machine to cut metal. BuyCNC as a leading supplier of CNC router machine and CNC laser cutting machine in China, we have a variety of machines that can cut metal, such as fiber laser cutting machine, CNC router cutting machine. waterjet cutting machine and so on.
Several common metal cutting methods
1.Grinding wheel cutting
The high-speed rotating grinding wheel is one of the best way to cut metal. It is a more common cutting method. The grinding wheel cutting machine is light and flexible, simple and convenient to use, and is widely used in various occasions, especially in construction sites and interior decoration. It is mainly used to cut some small diameter square tubes, round tubes, special-shaped tubes, etc.

2.Sawing cutting metal
The way of using a saw blade to cut a workpiece or material into slots for segmentation is called sawing. The sawing is performed by a metal band saw. Cutting off sheet metal materials is the most basic requirement of metal processing, so sawing machines are standard in the machining industry. The use of the sawing machine needs to select the appropriate saw blade according to the hardness of the material, and adjust the best sawing speed.
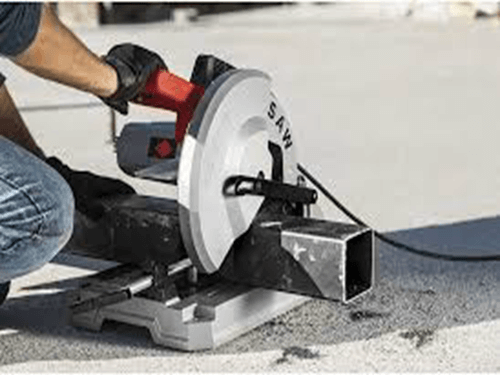
The above two methods of cutting metal (grinding wheel cutting and saw cutting) are generally used in household metal cutting and small metal processing factories. They can only perform the most basic simple cutting of metal, and cannot perform complex cutting.Next I will introduce you Some best way to cut metal which is more popular on the market now.
3.Laser metal cutting
Laser cutting is to irradiate the workpiece with a focused high-power density laser beam to quickly melt, vaporize, ablate or reach the ignition point of the irradiated material. At the same time, the molten material is blown away by the high-speed airflow coaxial with the beam to realize the cutting of the workpiece. open. Now generally use CO2 pulse laser and fiber laser cutting machine. Laser cutting is one of the thermal cutting methods, usually used for high-efficiency and precision cutting of thin steel metal plates (<30mm).
The cutting quality of the laser is excellent, not only the cutting speed is fast, but the dimensional accuracy is also high (up to ±0.05mm), and because the laser beam acts on a very small area, the heat-affected zone is very small, and the workpiece is hardly deformed.In terms of cutting quality, laser is better than plasma; in terms of cutting speed, plasma is faster than laser.
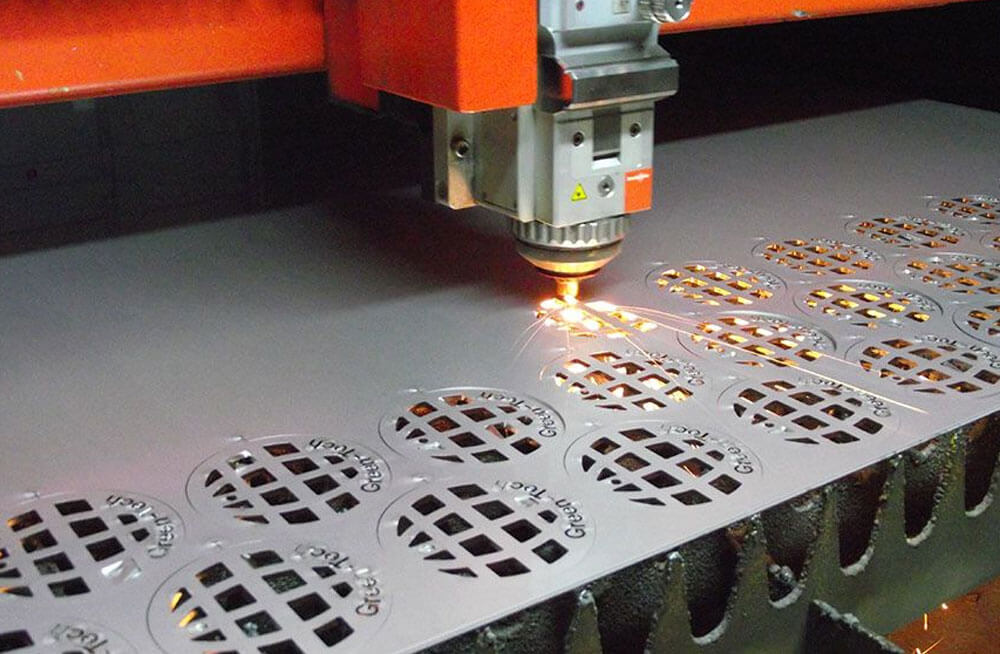
4.Flame cutting (gas cutting)
The process of flame cutting uses a chemical reaction between oxygen and hot steel to heat the metal, soften it and finally melt it. The heating gas is mostly acetylene or natural gas.
Flame cutting can only cut carbon plates, and is not applicable to other types of metals, such as stainless steel or copper and aluminum.
The advantage of flame cutting is low cost, and the maximum cutting thickness can reach two meters. The disadvantage is that the heat-affected zone and the thermal deformation are relatively large, the section is rough and there are more dross.Considering the subsequent processing, more allowance should be made.
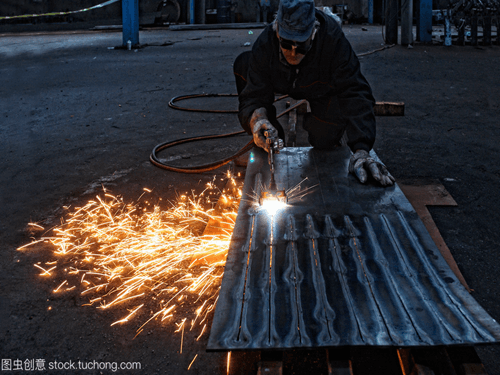
5. Plasma cutting
The plasma cutting method was invented in the 1950s. It uses the heat of a high-temperature plasma arc to locally melt (and evaporate) the metal at the incision of the workpiece, and use the momentum of the high-speed plasma to remove the molten metal to form an incision.
Plasma is generally used to cut materials with a thickness of less than 100mm. Unlike flame cutting, plasma cutting is fast, especially when cutting ordinary carbon steel sheets, the speed can reach 5-6 times that of oxygen cutting, and the cutting surface is smooth, thermal deformation is small, and heat-affected zones are less. Plasma cutting is not limited to cutting carbon plates, stainless steel, copper-aluminum materials and nickel-titanium metals, etc., can be competent.
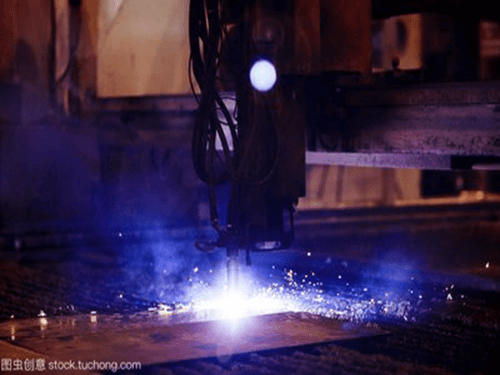
6.Waterjet cutting:
The plasma cutting method was invented in the 1950s. It uses the heat of a high-temperature plasma arc to locally melt (and evaporate) the metal at the incision of the workpiece, and use the momentum of the high-speed plasma to remove the molten metal to form an incision.
Plasma is generally used to cut materials with a thickness of less than 100mm. Unlike flame cutting, plasma cutting is fast, especially when cutting ordinary carbon steel sheets, the speed can reach 5-6 times that of oxygen cutting, and the cutting surface is smooth, thermal deformation is small, and heat-affected zones are less. Plasma cutting is not limited to cutting carbon plates, stainless steel, copper-aluminum materials and nickel-titanium metals, etc., can be competent.
At present, waterjet cutting is mainly used in the destruction of aerial bombs, petrochemical pipeline cutting, hazardous materials processing, and flammable and explosive materials cutting operations. The application effect is obvious, and the hidden safety hazard can be easily eliminated during the cutting process. It has become the first choice for aerial bomb destruction, petrochemical pipeline cutting, oil tank cutting, and oil tanker drilling.
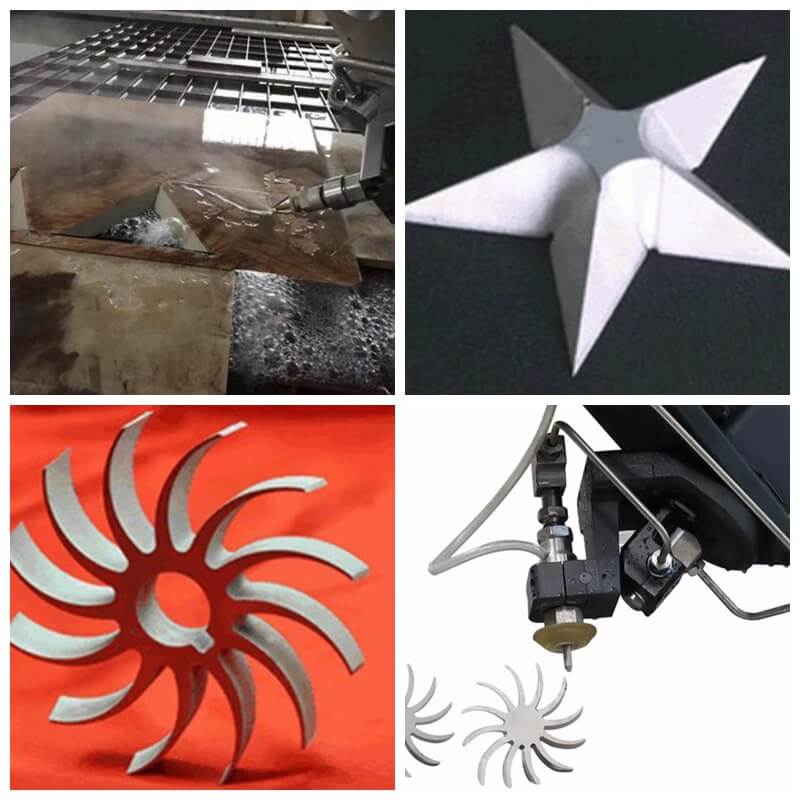
The Features of Serveral Best way to cut metal
Above we introduced some best way of how to cut sheet metal, but in actual operation, users often face the problem of how to choose the most suitable metal cutting process. In fact, the current mainstream metal cutting process has its own characteristics in terms of cutting thickness, cutting accuracy, metallurgical performance and production efficiency. We have summarized some of the more common problems and hope to help you
1. Equipment purchase cost
The above several cutting methods need to be equipped with different numerical control CNC, dust removal equipment, CAD/CAM software, etc. For example, compared to the slower cutting speeds of water jets and flames, lasers require higher speed and precision on thin plates. These requirements will directly lead to huge differences in equipment costs.
2. Cutting thickness comparison
The industrial application of laser cutting carbon steel is generally below 20mm. The cutting capacity is generally below 40mm. The industrial application of stainless steel is generally below 16mm, and the cutting capacity is generally below 25mm. And as the thickness of the workpiece increases, the cutting speed decreases significantly.
The thickness of waterjet cutting can be very thick, 0.8-100mm, or even thicker materials.
The plasma cutting thickness is 0-120mm, and the best cutting quality range is about 20mm. The plasma system has the highest cost performance.
The thickness of wire cutting is generally 40-60mm, and the thickest can reach 600mm.
3. Cutting speed comparison
If we use a laser cut machine with a power of 1200W to cut 2mm thick low-carbon steel plates, the cutting speed can reach 600cm/min; for 5mm thick polypropylene resin plates, the cutting speed can reach 1200cm/min. The cutting efficiency that can be achieved by wire EDM is generally 20-60 mm2/min, up to 300 mm2/min; obviously, the laser cutting speed is fast and can be used for mass production. The water cutting speed is quite slow and not suitable for mass production.
4. Comparison of cutting accuracy
The laser cutting incision is narrow, the two sides of the slit are parallel and perpendicular to the surface, and the dimensional accuracy of the cut parts can reach ±0.2mm.
The plasma cutting machine can reach within 1mm.
Water cutting will not produce thermal deformation, and the accuracy is ±0.1mm. If a dynamic waterjet machine is used, the cutting accuracy can be improved, and the cutting accuracy can reach ±0.02mm, eliminating the cutting slope.
5.Comparison of slit width
Laser cutting is more precise than plasma cutting, and the slit is small, about 0.5mm.
The slit of plasma cutting is larger than laser cutting, about 1-2mm.
The cutting seam of water cutting is about 10% larger than the diameter of the knife tube, generally 0.8-1.2mm. As the diameter of the sand knife tube expands, the incision becomes larger.
6. Comparison of production input cost
Different models of laser cutting machines have different prices. Cheap ones such as carbon dioxide laser cutting machines cost only about 7000 dollars, and expensive ones such as 1000W fiber laser cutting machines cost 15,000 to 40,000 dollars.
Plasma cutting machines are much cheaper than laser cutting machines. Depending on the power and brand of the plasma cutting machine, the price is different and the cost of use is higher. Basically, as long as it can cut conductive materials.
The equipment cost of waterjet cutting machine is second only to laser cutting, with high energy consumption and high maintenance cost. The cutting speed is not as fast as plasma, because all abrasives are disposable, and they are discharged into the nature once used. , So the environmental pollution caused is also more serious.
7. Cutting cost per unit part or unit length
This cost includes gas, nozzle, electrode, electricity and water, etc. In some cases, equipment purchase costs and labor costs (such as loading and unloading) are also shared. So be sure to pay attention to its scope when making comparisons. Compared with the unit time cost, the unit part or unit length cost covers the cutting speed and production efficiency, and has more practical reference value.
8. Ease of use
This requirement mainly lies in software (especially CAM) and CNC numerical control. Now through the integration of professional experience to shorten the learning time and reduce the dependence on experience. For example, Haibao, the leader in the field of plasma cutting, directly built the full set of process parameters of Haibao plasma into Haibao’s own nesting software and CNC numerical control. New users can quickly grasp it and maintain the same cutting quality and production as professional veterans. effectiveness. Although this demand is difficult to quantify, it cannot be ignored in actual production.
BuyCNC provides a variety of metal cutting tools, including but not limited to: CNC router machine for metal, laser metal cutting machine, plasma metal cutting machine, waterjet cutting machine. If you want to know more about these machines, please leave your Contact information, we will reply you as soon as possible.