Mach3 CNC Router Controller Table of Contents
What is the Mach3 CNC Router Software
The CNC system is the control core of the CNC router machine. The performance of the control system directly affects the processing quality and efficiency of the cutting machine. Therefore, a stable, efficient and cost-effective control system is one of the factors that must be considered when buying a CNC cutter. The Mach3 CNC router controller is developed by ArtSoft that based on Windows. Speaking of the Mach3 CNC controller, it is necessary to explain CNC engraving machinery’s input and output devices. The input and output of the CNC cutting machine use the LPT or USB port of the PC. The principle of Mach3 software is to control the stepper motor or servo motor driver by outputting pulse and direction signals to realize the control of the CNC engraving machine router’s movement on the X Y Z-axis.
The Mach3 CNC router controller version currently supported is WIN XP or WIN2000.Mach3. Besides, the Mach3 CNC machine controller has a wide range of applications in the CNC engraving industry. The Mach3 software supports all international standard G codes and can control three-axis, four-axis, five-axis, and even six-axis CNC cutting machine parts. The machining accuracy of the Mach3 CNC controller can reach 0.0001MM, which fully realizes the high-precision machining of complex materials. Mach3 software has certain restrictions on the number of G code lines that can be executed. Even the authorized version can execute G code lines up to 10,000,000 lines, but this is enough for simpler and conventional workpiece processing.
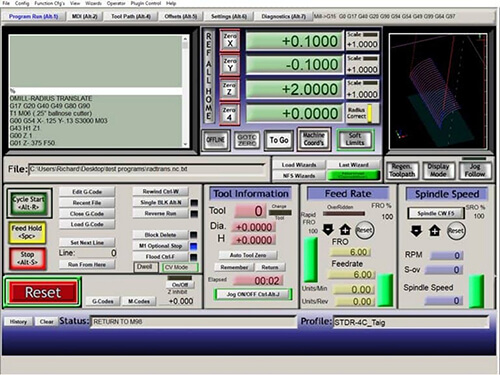
As we all know, the CNC cutting machine’s operation is inseparable from the CNC control system. The CNC engraving machine’s current control system can be roughly divided into computer control, handle control, and integrated machine control. Mach3 CNC controller is a computer control system, and a computer mainly controls the CNC engraving machine during work. Specifically, the Mach3 CNC controller links the computer and the CNC cutting machine and outputs from the computer to control the CNC engraving machine’s work. Besides, software that can replace the Mach3 CNC controller includes DSP, Nc-studio, etc.
The DSP CNC controller’s working principle is to make a path on the existing computer and save it on the device and then insert the storage device into the DSP handle. Finally, the DSP handle is connected to the cutting machine to control the CNC engraving machine. Although the DSP control system is simple to operate, it is inconvenient to modify the path that has been made. The Mach3 control system has strong control ability, high precision and excellent performance, and is recognized as the core technology of CNC engraving machine. Most of our cutting machines use Mach3 CNC machine controller.
How Much of The Mach3 CNC Router Controller
Generally, the CNC cutting machines purchased have their own Mach3 CNC controller. They do not require extra pay. If the built-in Mach3 CNC controller is not easy to use, or the CNC controller operation is stuck or not smooth, it is recommended to purchase a genuine Mach3 CNC controller for replacement. There are many reasons for the system’s failure, including the computer configuration of the installation system.
Therefore, before purchasing the Mach3 CNC controller, you must understand the operating environment that the software is suitable for. In the following, we will explain the operating environment suitable for the Mach3 CNC controller. For any CNC engraving machine purchased at BuyCNC, we provide free installation and training services for the Mach3 CNC controller and update the Mach3 software for free in time with its development and upgrade. This will be very convenient for your operation and worry-free after-sales.
What impact does the Mach3 CNC controller have on the CNC engraving machine industry?
The CNC engraving machine is the product of the combination of CNC cutting technology and the engraving process. The CNC cutter executes the corresponding processing program code through the Mach3 CNC controller to control the machine to complete the engraving action. Compared with the traditional CNC engraving machine, the cutting machine equipped with a Mach3 CNC controller has the following advantages:
① High degree of automation. The entire cutting process is automatically completed by the CNC engraving machine, without manual operation.
②The product has high dimensional accuracy. The cutting process is controlled by a computer, which can achieve high precision and quality. When processing materials in batches, the product has a good consistency.
③Expand the field of carving. The Mach3 CNC controller can execute various corresponding processing codes and use various tools to realize the cutting processing of reliefs and various complex curved surfaces. Thereby improving the engraving efficiency.
What is the Principle of Mach3 CNC Router Controller
The Mach3 CNC controller of the CNC engraving machine is a kind of trajectory control system object, an automatic control system for coordinated movement of each axis. Essentially, it is controlled by the displacement of each movement axis. The basic working process of Mach3 CNC controller is:
1.The First Step:
digitize the graphics to be processed through the CNC software, and generate processing path information. The processing path information is transmitted to the CNC controller through a certain data transmission method.
2.The Second Step:
Mach3 CNC controller processes the processing path information, generates control commands and sends them to each motion axis. Coordinate the X, Y, Z three-coordinate axis movement, the CNC engraving machine spindle and auxiliary actions to realize the relative movement of the tool and the processed workpiece and automatically complete the processing process.
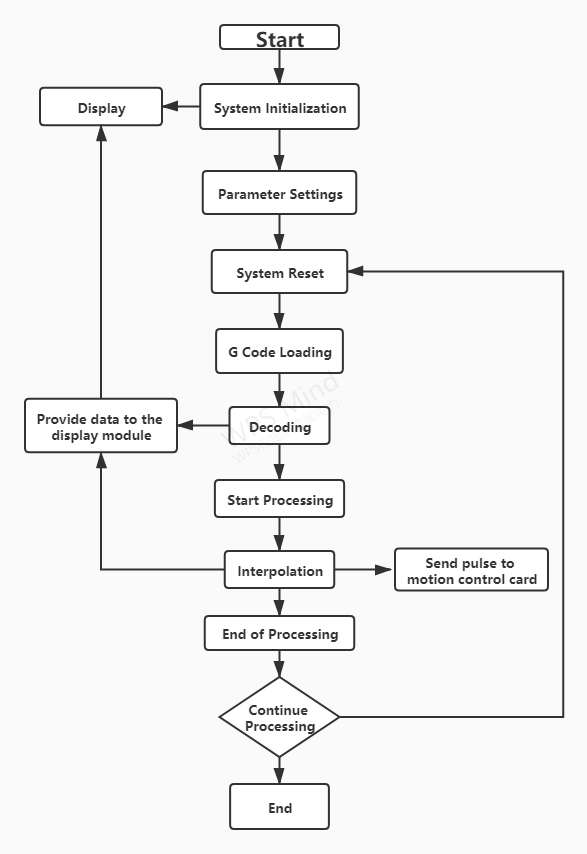
Therefore, the CNC engraving machine can engrave the plane, text or three-dimensional graphics designed in the Mach3 CNC controller. So it can realize the automatic cutting process.
What are the Functions of Mach3 CNC Router Controller
As a special CNC machine, the CNC engraving machine is very similar to the CNC machine in terms of control principles and functions. However, due to the small forming area, low efficiency, and long processing tool path of the engraving processing, the CNC controller has a certain particularity. Therefore, the main functions of the cutting machine Mach3 CNC controller are introduced here in detail.
1. Loading and preprocessing of processing code.
The first step of the CNC engraving machine Mach3 CNC controller is the loading and preprocessing the code, which guarantees the smooth process and extracts the information required for CNC processing. This process’s input is the processing code file, and the output is the processing command data set obtained after analysis and processing.
2. Motion control.
The CNC engraving machine’s movement is mainly completed by coordinating X-axis, Y-axis, Z-axis, and spindle. According to the processing data obtained after analyzing the processing code, the Mach3 CNC controller controls each movement axis’s coordinated movement to complete the engraving processing. The X and Y axes produce synthetic motion, and the Z-axis controls the tool’s cutting depth. Therefore, one of the basic control functions of the Mach3 CNC controller is to realize the motion control of the X, Y, and Z coordinate axes.
3. Speed control.
The Mach3 CNC system’s speed control is mainly embodied in two aspects: rapidity and speed forward-looking processing capabilities. For processing requirements with small processing areas, long motion lines, and frequent start and stop, the control system requires rapidity in command operation, motion speed, and acceleration. The Mach3 CNC controller has this rapidity. The speed-forward processing capability of the Mach3 CNC controller refers to reducing the feed speed before a sudden change in the processing direction, thereby avoiding or reducing the impact on the machine tool’s moving parts.
4. Spindle control.
The spindle speed is adjusted by PWM pulse width. And the range of the speed is 0-22000rpm. When the spindle speed is high, the cutting speed of the tool is also high. The Mach3 CNC controller’s effective control improves the tool’s cutting ability and facilitates obtaining a better part surface finish. However, limited by the material of the processed parts and tools, sometimes low-speed machining avoids affecting tool life. Therefore, it has a wide range of speed adjustments to help users adjust the spindle speed according to different conditions.
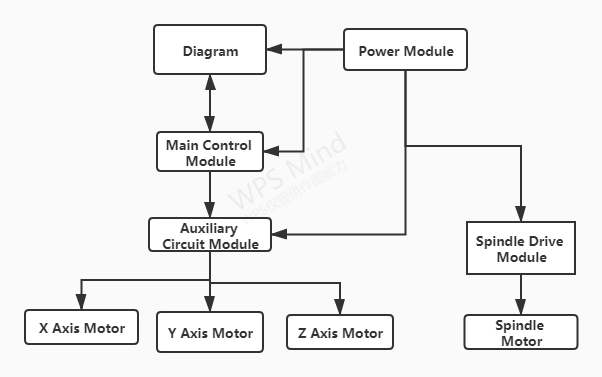
5. Drive control accuracy.
The minimum pulse equivalent of X, Y, Z axial motion control is 1.25um.
6. High-speed interpolation calculation.
Between the starting point and the processing curve’s endpoint, the Mach3 CNC controller uses a certain algorithm to densify the data points. It decomposes them into each coordinate axis’s movement, which is converted into a command to control each coordinate axis’s movement.
7. Economy.
On the premise of ensuring the powerful functions, stable performance, and high processing efficiency of the CNC engraving machine, the Mach3 CNC controller’s cost is low, making it have better cost performance and market competitiveness.
What are the characteristics of the Mach3 CNC router controller?
The CNC engraving machine equipped with the Mach3 CNC controller will have many errors during the operation. This article has made a unified operation instruction for the recent problems raised by customers and sorted out the characteristics of the Mach3 CNC controller:
- The CNC engraving machine must be equipped with a manual control device and an emergency stop button.
- The tools of the CNC engraving machine need to be perpendicular to each other.
- The origin of the tool installation of the CNC engraving machine is consistent with the workpiece.
- Find the button where the tool is at the origin.
- The button to ensure that the tool is controllable at the associated motion’s limit speed.
- The spindle can drive the tool to rotate.
- The CNC engraving machine has no less than three additional axes.
- The CNC engraving machine can realize the interlocking of the protective device.
- The spray mode of the cooling liquid of the CNC engraving machine is controllable.
- The tool post has a digital detection function encoder, which can display machine tool parts’ position.
Computer configuration was suitable for Mach3 CNC controller operation
The Mach3 CNC controller’s convenience makes more and more CNC engraving machine suppliers choose it to control the operation of large machinery. Similarly, the Mach3 CNC controller also puts forward certain requirements on the configuration of the computer. When purchasing the Mach3 CNC controller, you need to check the computer configuration supported by the software. The following data is for your reference.
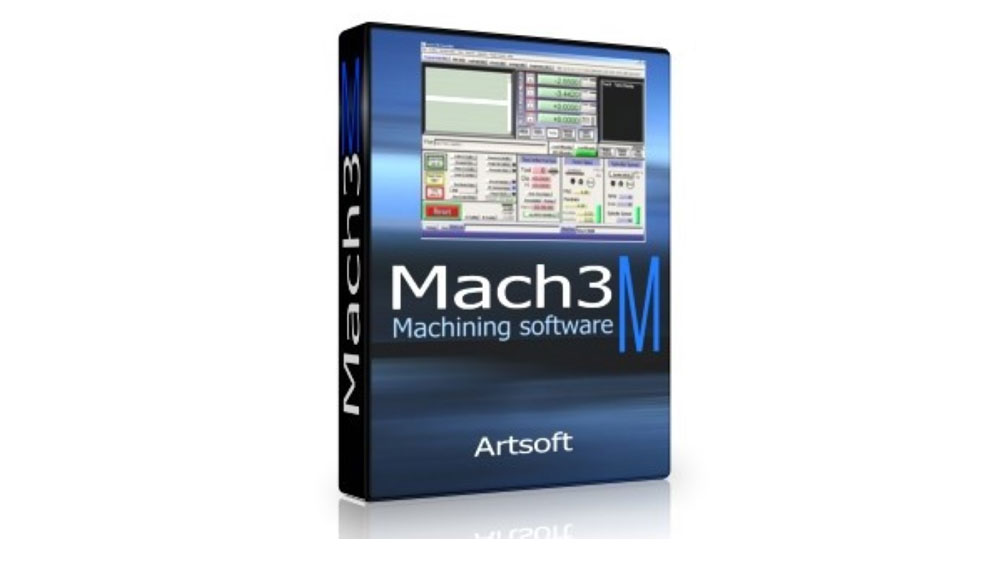
Requirements when using external motion equipment for machine control:① Appropriate external motion controller.
②Windows 2000, Windows XP, Windows Vista, Windows 7, Windows 8 and Windows 10 desktop or laptop computers.
③1Ghz CPU.
④512MB memory.
⑤Video card with 32MB RAM.
Requirements for using the parallel port for machine control: | ①A desktop computer with at least one parallel port (laptop computers are not supported). ②32-bit version of Windows 2000, Windows XP, Windows Vista or Windows 7. ③1Ghz CPU. ④512MB memory. ⑤ Non-integrated graphics card with 32MB RAM. (Large G-code files, especially 3D files will require a video card with 512MB RAM or higher) |