Sheet Metal Laser Cutting Machine

Sheet Metal Laser Cutting Machine
The sheet metal laserm cutting machine is a new type of cutting machine product newly invented in the international market in recent years. This cutting machine product has absolute advantages in cutting speed and mechanical volume. Today We mainly talk about the main advantages of this cutting machine in which aspects.
1. Advanced cutting technology
The cutting principle adopted by this new type of laser metal cutting machines is a high-performance laser cutter. During the cutting process, the laser emits countless high-performance, high-energy laser rays. The huge energy generated by these laser rays , The cut surface can be vaporized instantly, so that the very hard interface can be easily removed. At present, this process is still the most advanced cutting process, no other cutting process can surpass it, and this cutting process is very fast in the cutting process, and it can easily cut very thick steel plates in an instant, and cut The accuracy of the cutting is also very accurate, and the accuracy of the cutting cross section can reach a few millimeters, which can fully meet some high-demand cutting needs.
2. The size of the laser sheet metal cutters machine is very small
There is only one core component of this metal laser cutter, which is the laser that emits the laser. The laser is very small and does not occupy a lot of space like other cutting products of the same type, so the overall volume of the machine will be reduced. A lot of reduction, whether in the process of mechanical production or transportation, can reduce a lot of manpower and material resources for us.
3. Easy to operate
In the process of using fiber laser cutting machine, all information and energy transmission are transmitted through optical fiber. The biggest advantage of transmission in this way is that it saves a lot of manpower and material resources. Any light path leakage will occur. Moreover, you can easily transfer energy to the laser without making any optical path adjustments before using the equipment.
4. The cutting performance is very stable
This kind of laser cutter uses an extremely stable world-class laser in the cutting process. The service life of this kind of laser will be as long as several years, and in the process of use, except for human factors, there is almost no production. Any failure of the system itself, so even if this laser cutting machine is under long-term working pressure, it will not produce any vibration or other adverse effects.

Why the CO2 Laser Cutting Machine Was Eliminated
Nowadays, laser equipment changes with each passing day, and the pace of replacing old equipment with new equipment to become the new mainstream of the manufacturing industry is accelerating, such as fiber laser cutting machines instead of CO2 laser cutting machines. Why Fiber laser sheet metal laser cutting machine can replace CO2 laser cutting machine? Let’s analyze it from three aspects.
1. Maintenance costs are too high
CO2 laser cutting machine: the maintenance cost is high, the front mirror and the tail mirror are expensive, the life of the turbine bearing is short, and the replacement cost is high. Fiber metal laser cutting machine: maintenance-free, basically no consumables, and capable of handling harsh working environments, with a high tolerance for dust, shock, impact, humidity, and temperature.
2. Excessive processing cost
The photoelectric conversion rate of the CO2 laser cutting machine is much lower than that of the fiber laser cutting machine, and the laser tube is a consumer product. Under the same power, the fiber equipment can better use the laser to create value, so the processing cost of the fiber is lower. Of course, the purchase price of fiber optic equipment is higher than that of carbon dioxide equipment.
3. Complex technology
CO2 laser has complex structure, high maintenance cost, and large beam divergence during processing, which is not suitable for large-format processing. Although the cutting seam is relatively thin, the speed is very slow when processing thick plates. The laser characteristics of fiber laser cutting machine are embodied in miniaturization, intensiveness, high brightness and high conversion rate. For thin plate processing, the cutting speed of fiber laser cutting machine with the same power is 2-3 times higher than that of CO2, and the cutting section is smooth.
The above is the reason why the CO2 laser metal cutting machine is gradually eliminated. The reason why the fiber laser metal cutting machine can quickly gain a foothold in the market and gradually replace the traditional cutting process is precisely because of its various technical advantages, in order to realize the product The finishing process provides the necessary process technology.
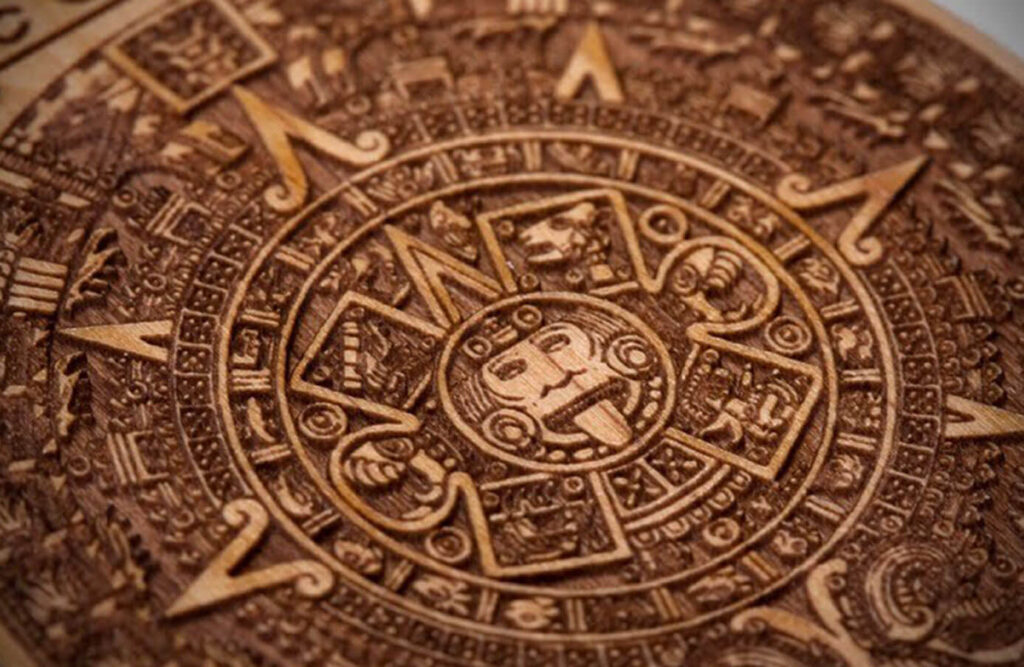
How to Debug the Metal Laser Cutting Machine?
With the rapid growth of output and consumption in my country’s metal industry, sheet metal processing technology has also developed rapidly, especially the advent of laser cutting machines, which has brought an unprecedented leap in sheet metal processing.
In fact, machines, like humans, require frequent maintenance to maintain a relatively good operating condition. If the machine cuts slowly or does not cut well, there are actually ways to adjust it. Today, I will introduce several ways to improve the cutting effect and speed of the laser cutting machine.
The laser metal cutter machine parameter setting is one of the main reasons that affect the cutting speed of the machine. Under normal circumstances, if the parameters are not adjusted well, its cutting speed will not work. So we have to set the machine parameters to get a faster cutting speed. When adjusting this parameter, generally pay attention to the following points:
Initial speed: As the name suggests, this setting is the speed at which the machine starts, which is like the speed at which the car is driving at the beginning. Many customers have such a misunderstanding that the greater the initial speed, the better, but in fact this is wrong. If the initial speed of the laser machine is set too high, the machine jitter will be very large.
Acceleration: Acceleration means the speed of the accelerator when the car is driving. It is the time it takes from the initial speed to the normal cutting of the machine. When the machine is cutting different patterns, it is a process of constantly starting, stopping, and stopping. If the acceleration setting is too low, the cutting of the machine will slow down.
2.Install the accessories of the laser metal cutting machine
Rail installation:
The guide rails should be installed in parallel. If the installation is not parallel, the machine will have resistance when running, it will be stuck when it is walking, and there will be saw teeth when it is cut. Therefore, the two guide rails in the Y direction can be installed in two parallel lines, and there can be no error between them.
Beam installation:
The beam and coupling are not properly installed. When the machine beam and coupling are installed, the screw is not locked, or the lock is oblique, etc., it will happen.
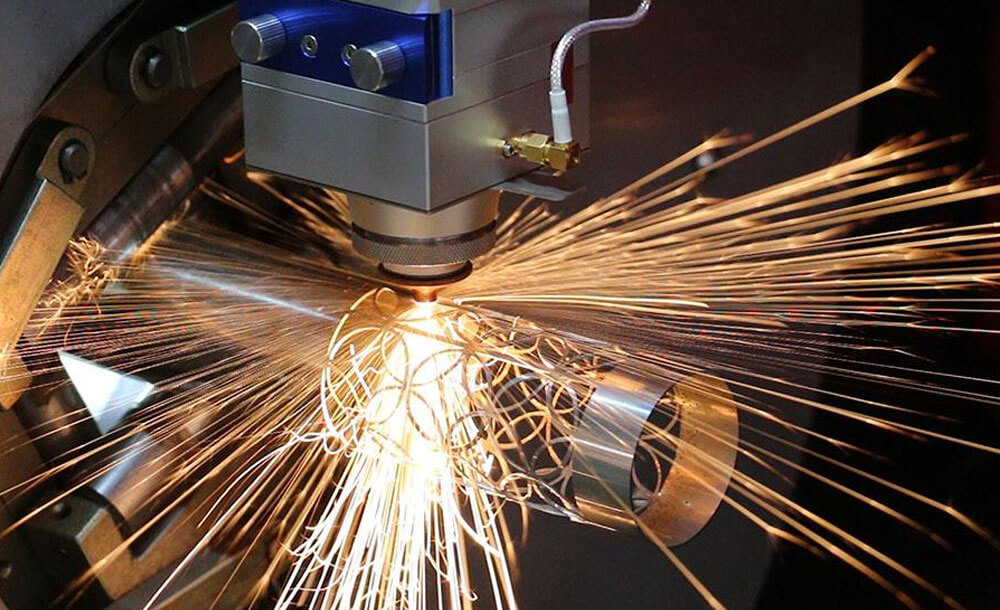
Problems About Laser Sheet Metal Cutters
It is expected that the metal laser cutting machine has problems in the processing process. If the problem is not solved in time, it will definitely affect the work efficiency. Therefore, after the problem occurs, the manufacturer needs to provide customers with effective Solution, how should we solve the more common problems?
1. Deformation of small holes in laser processing
This is because the laser sheet metal cutter machine (only for high-power laser cutting machines) does not use blasting perforation when processing small holes, but uses pulse perforation (soft puncture), which makes the laser energy in a small The area is too concentrated, and the non-processing area is also scorched, resulting in hole deformation and affecting processing quality. At this time, we should change the pulse perforation (soft puncture) method to the blast perforation (ordinary puncture) method in the processing program to solve it. The opposite is true for laser cutting machines with lower power. Pulse perforation should be used to obtain a better surface finish when processing small holes.
2. The process of metal laser cutting machine is unstable
The main situation of unstable processing: the choice of the laser head nozzle does not match the thickness of the processed plate; the laser cutting line speed is too fast, and the operation control is required to reduce the line speed. Secondly, the inaccurate nozzle induction leads to the excessive laser focus position error, which needs to be re- Detecting nozzle sensing data is easy to appear when cutting aluminum.
3. Abnormal sparks appear when the metal laser cutting machine cuts low carbon steel
The appearance of such a phenomenon affects the processing quality of the cut section finish. At this time, when other parameters are normal, the following conditions should be considered: the loss of the laser head nozzle, the nozzle should be replaced in time. In the case of no new nozzle replacement, the cutting working gas pressure should be increased; the thread at the connection between the nozzle and the laser head is loose. At this time, the cutting should be suspended, check the connection status of the laser head, and then re-install the thread.
4. When the metal laser cutting machine is cutting low-carbon steel, burrs appear on the workpiece
The upper and lower positions of the laser focus are not correct, you need to do a focus position test, and adjust according to the offset of the focus; the output power of the laser is not enough, you need to check whether the laser generator is working normally, if it is normal, observe the output value of the laser control button If it is correct, adjust it; the cutting line speed is too slow, and the line speed needs to be increased during the operation control; the purity of the cutting gas is not enough, and high-quality cutting working gas needs to be provided; the laser focus is offset, and the focus position test needs to be done according to the focus Adjust the offset of the machine tool; the instability of the machine running time is too long, and the machine needs to be shut down and restarted at this time.