Table of Contents
Laser welding machine technology has attracted more and more attention in the manufacturing industry due to its advantages such as high precision, high efficiency, low deformation, environmental protection and energy saving. However, the suitability of best welder varies for different customers and products. When deciding whether to use laser welding machine technology, we need to fully consider its advantages and disadvantages, as well as the specific needs of the product.
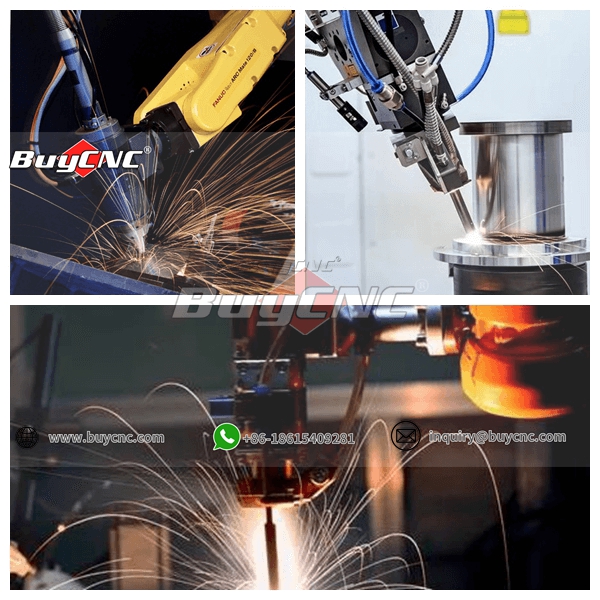
The main advantages of best welder are as follows:
Laser welding machine has high energy density.
First of all, laser welding machine has high energy density, which can quickly heat and melt materials, achieving high-speed and efficient welding. This gives laser welding machine a significant advantage when processing large quantities of products and can significantly improve production efficiency.
The penetration depth of best welder is small
Secondly, laser welding machine has small penetration depth and small deformation. Since the heating area of laser welding machine is very small and the heat affected zone is also very small, the deformation and residual stress after welding are small. This helps maintain the original shape and dimensional accuracy of the product.
In addition, the weld quality of laser welding machine is high. The weld seam of laser welding machine has good shape, stable size and few defects, and can achieve high-precision welding. This is undoubtedly a huge advantage for products that have strict requirements on welding quality.
Best welder is environmentally friendly and energy-saving
In addition to the above advantages, laser welding machine also has significant performance in environmental protection and energy saving: In terms of environmental protection, laser welding machine technology has significant advantages. Traditional welding methods often require the use of flux or filler materials, which can produce harmful fumes and exhaust gases during use. In contrast, laser welding machine does not require the use of welding flux, and no open flames and smoke are generated during the welding process, thus reducing the emission of harmful substances and reducing environmental pollution. In addition, laser welding machine can also accurately control the position and energy of the welding point, reducing the generation of waste materials and further improving environmental performance.
In terms of energy saving, best welder also performs well. laser welding machine equipment has high energy conversion efficiency and can convert most of the electrical energy into laser energy, which can be directly used to melt materials. In contrast, traditional welding methods may suffer from low energy utilization efficiency, with part of the energy lost in the form of heat. Therefore, laser welding machine has significant advantages in energy saving, helping to reduce production costs and energy consumption.
Disadvantages of best welder
However, laser welding machine also has some shortcomings and shortcomings. First of all, laser welding machine equipment is relatively expensive, and the requirements for interface processing, assembly, and positioning of welding parts are very high. This increases the initial investment cost of the equipment and may increase the skill requirements on the operator. Secondly, laser welding machine may produce defects such as spatter, cracks, and pores under certain circumstances, which may have a negative impact on the surface quality and structural strength of the weld.

To sum up, laser welding machine has many advantages, such as high efficiency, high precision, low deformation, environmental protection and energy saving. However, there are also some shortcomings and shortcomings that need to be considered when applying it. When deciding whether to use laser welding machine technology, we need to comprehensively consider factors such as product material, thickness, shape, structure, production batch, cost requirements, safety and environmental protection. At the same time, we also need to evaluate the investment cost, operating difficulty, and possible defects of laser welding machine equipment. Only by comprehensively considering these factors can we ensure that we choose the most suitable welding method for our customers’ products.