Table of Contents
The Development And Principle of Laser Cleaning
Traditional industrial cleaning methods mainly include high-pressure water, chemical reagents, ultrasonic waves, and mechanical grinding. However, these cleaning methods have problems such as damage to the substrate, poor working environment, pollution, incomplete cleaning of some locations, and high cleaning costs.
With the intensification of environmental pollution, scholars from all over the world are actively developing new cleaning technologies that are energy-saving, environmentally friendly and efficient.
Because laser cleaning technology has the advantages of low damage to the matrix material, high cleaning precision, zero emission and no pollution, it is gradually being valued and favored by academia and industry. There is no doubt that the application of laser cleaning technology to the cleaning of dirt on metal surfaces has a very broad prospect.
Development and Status of Laser Cleaning Technology
In the 1960s, the famous physicist Schawlow first proposed laser cleaning, and then applied the technology to the restoration and maintenance of ancient texts. The decontamination range of foreign laser cleaning is very wide, from thick rust layer to fine particles on the surface of objects can be removed, including the cleaning of cultural relics and artworks, the removal of rubber contamination on the surface of tire molds, the removal of silicone oil contamination on the surface of gold film, and the removal of microelectronics High-precision cleaning in the industry.
In China, laser cleaning machine really started in 2004, and China began to invest a lot of manpower and material resources to strengthen the research on laser cleaning technology. In the past ten years, with the development of advanced lasers, from inefficient and bulky carbon dioxide lasers to light and compact fiber lasers; from continuous output lasers to nanosecond or even picosecond, femtosecond short pulse lasers; from visible light output To the output of long-wave infrared light and short-wave ultraviolet light… The laser has made a leap in energy output, wavelength range, laser quality, and energy conversion efficiency.
The development of lasers has naturally also promoted the rapid development of laser cleaning technology, and laser cleaning technology has achieved fruitful results in theory and application.
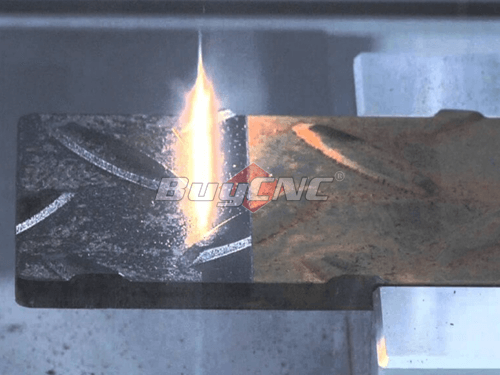
The Principle Of Laser Cleaning Technology
The process of pulsed laser cleaning relies on the properties of the light pulses produced by the laser, based on photophysical reactions caused by the interaction between the high-intensity beam, the short-pulse laser, and the contamination layer. Its physical principles can be summarized as follows:
a) The beam emitted by the laser is absorbed by the contamination layer on the surface to be treated
b) The absorption of large energy forms a rapidly expanding plasma (highly ionized unstable gas), resulting in a shock wave
c) The shock wave breaks the contaminants into fragments and is rejected
d) The optical pulse width must be short enough to avoid heat build-up that would destroy the treated surface
e) Experiments show that when there is oxide on the metal surface, the plasma is generated on the metal surface
Plasma is only generated when the energy density is above a threshold, which depends on the contamination or oxide layer being removed. This threshold effect is important for effective cleaning while keeping the substrate material safe.
There is also a second threshold for the appearance of plasma. If the energy density exceeds this threshold, the substrate material will be destroyed. In order to carry out effective cleaning on the premise of ensuring the safety of the substrate material, the laser parameters must be adjusted according to the situation, so that the energy density of the light pulse is strictly between the two thresholds.
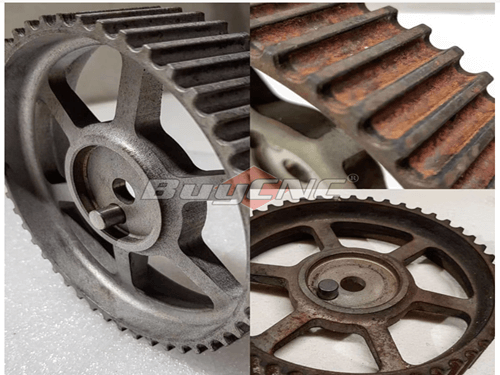
Advantages Of Laser Cleaning
Compared with traditional cleaning methods such as mechanical friction cleaning, chemical corrosion cleaning, liquid solid strong impact cleaning, and high-frequency ultrasonic cleaning, laser cleaning has five obvious advantages:
Environmental advantages: Laser cleaning is a “green” cleaning method, without the use of any chemicals and cleaning fluids, and the cleaned waste is basically solid powder, small in size, easy to store, recyclable, no photochemical reaction, no pollution will occur.
Effect advantage: The traditional cleaning method is often contact cleaning, which has a mechanical force on the surface of the cleaned object, damages the surface of the object or the cleaning medium adheres to the surface of the object to be cleaned, and cannot be removed, resulting in secondary pollution. Laser cleaning has no effect. Abrasive and non-contact, no thermal effects do not damage the substrate, making these problems easy.
Control advantages: The laser can be transmitted through the optical fiber, cooperate with the robot hand and the robot, and can easily realize long-distance operation. It can clean the parts that are not easy to reach by traditional methods, which can ensure the safety of personnel when used in some dangerous places.
Convenience advantage: Laser cleaning can remove various types of contaminants on the surface of various materials, and achieve cleanliness that cannot be achieved by conventional cleaning. It can also selectively clean contaminants on the surface of the material without damaging the surface of the material.
Cost advantage: Laser cleaning is fast, efficient, and time-saving; although the initial one-time investment in purchasing a laser cleaning system at this stage is high, the cleaning system can be used stably for a long time, with low operating costs, and more importantly, it can be easily automated. . It can be predicted that the cost of laser cleaning system will be greatly reduced in the future, thereby further reducing the cost of using laser cleaning technology.
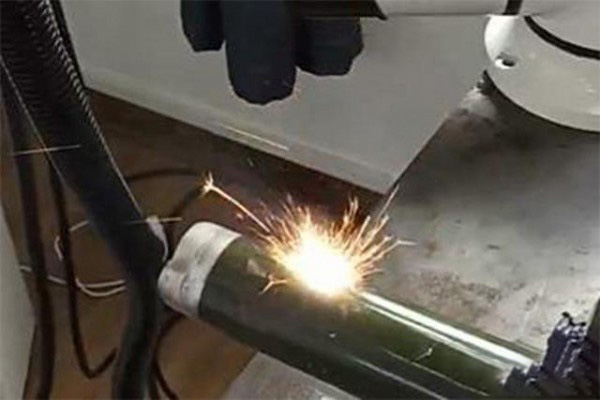
Classification of Laser Cleaning Technology
Laser cleaning methods can be mainly divided into the following three categories:
1. Laser dry cleaning
Direct decontamination by laser radiation. After the laser is absorbed by objects or dirt particles, vibration is generated to separate the substrate and the contaminants. There are two main ways to remove dirt particles in laser dry cleaning: one is the instantaneous thermal expansion of the surface of the substrate, which generates vibration, so that the particles adsorbed on the surface are removed. The other is the thermal expansion of the particles themselves, which causes the particles to leave the surface of the substrate.
2. Laser Wet Cleaning
Laser wet cleaning is to first uniformly cover a layer of liquid dielectric film on the surface of the substrate to be cleaned, and then use laser radiation to remove stains. According to the absorption of the laser by the dielectric film and the substrate, wet cleaning can be divided into strong substrate absorption, strong dielectric film absorption, and dielectric film substrate common absorption. In the case of strong matrix absorption, after the matrix absorbs the laser energy, the heat is transferred to the liquid medium film, the liquid layer at the interface between the matrix and the liquid is overheated and boiled, and the liquid layer and the stain are removed together.
3. Laser + inert gas cleaning
At the same time as the laser is irradiated, an inert gas is blown to the surface of the workpiece. When the contaminants are peeled off from the surface, they are blown away from the surface by the gas to prevent the clean surface from being polluted and oxidized.
Laser Cleaning Machine For Sale
