Table of Contents
We all know that there are various cleaning methods in the industrial manufacturing field, mostly using chemical agents and mechanical methods. However, in the process of cleaning, chemical cleaning often still has residues, and the types of chemicals that can be used in industrial production cleaning will become less and less.
In the industrial field, according to the different cleaning media, it can be divided into wet cleaning and dry cleaning: generally, the cleaning in the liquid medium is called wet cleaning, and the cleaning in the medium is called dry cleaning. Most of the traditional cleaning methods are wet cleaning, but with the rapid development of science and technology.
In recent years, laser clean technology has been used more and more widely, and we have also brought laser technology into industrial cleaning. Among them, dry cleaning, including laser cleaning, has developed rapidly in the field of high-precision industrial technology. It can be concluded from the latest data that new technologies are constantly being applied in the industrial field.
Principle of Laser Cleaning Machine
Nowadays, with the rapid development of industrial lasers in China, laser cleaning technology is undoubtedly a high-energy laser process for cleaning metal workpieces in the industrial field. Laser cleaning technology has the characteristics of no grinding, non-contact, no thermal effect and suitable for all kinds of materials. Laser cleaning can solve the problems that cannot be solved by wet cleaning.
Laser cleaning is to use the characteristics of laser beam, such as large energy density, controllable direction and strong convergence ability, to destroy the binding force between pollutants and matrix or to remove pollutants by direct gasification, so as to reduce the binding strength between pollutants and matrix, so as to achieve the effect of cleaning the workpiece surface. The principle of laser cleaning is shown in the figure below.
When the pollutant on the surface of the workpiece absorbs the energy of the laser, its rapid gasification or instantaneous thermal expansion overcomes the force between the pollutant and the substrate surface. Due to the increase of heating energy, the pollutant particles vibrate and fall off from the substrate surface.
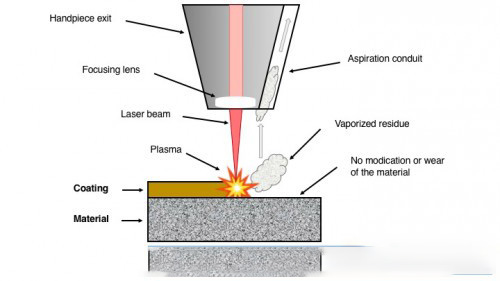
Application Of Laser Cleaning Machine
As a pre-processing procedure in industrial production, laser cleaning machine can not only effectively remove rust, decontamination, etc., but also chemically react on the surface of the substrate to form a protective layer to prevent the substrate from rusting again and improve its corrosion resistance. At present, laser cleaning machines have been applied to various fields such as military industry, mold cleaning, surface treatment, microelectronics, cultural relics protection and medical treatment. Especially the following industries are widely used
1. Metal or glass surface coating removal, rapid paint stripping;
2. Rapid rust removal, as well as various oxides;
3. Remove grease, resin, glue, dust, stains and production residues;
4. The metal surface is roughened;
5. Paint stripping, rust removal, oil removal, oxidation and residue treatment after welding before welding or bonding.
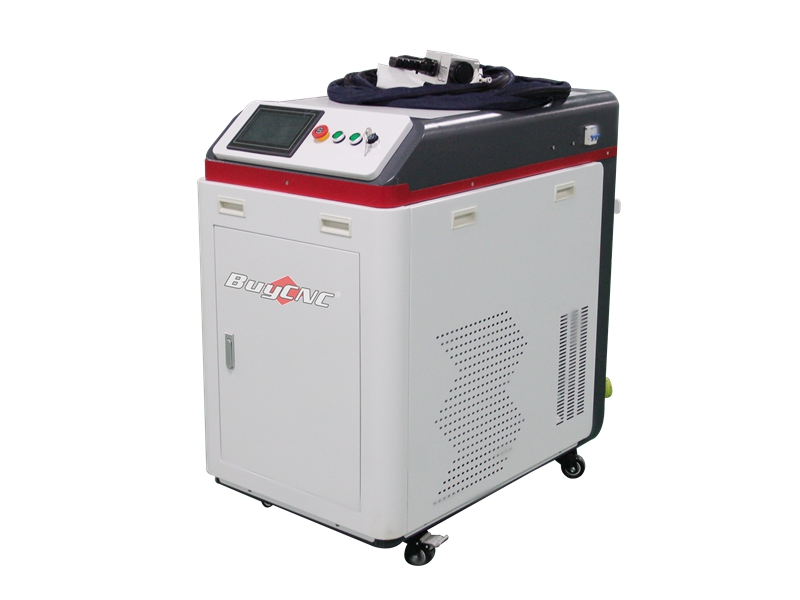
Light Source Control of Laser Cleaning
In order to optimize the effect of laser cleaning on the surface of the cleaned object, it is necessary to comprehensively consider the laser cleaning method, cleaning model, laser wavelength, energy density, power, pulse frequency, pulse time, laser incidence angle and other process parameters.
Pulsed laser can effectively clean the rust on the surface of carbon steel. Only by systematically studying the process parameters can an efficient laser cleaning system be formed. For example, pulse width: laser cleaning can change the grain structure and orientation of the substrate surface without damaging the substrate surface, and can also control the surface roughness of the substrate, so as to enhance the comprehensive performance of the substrate surface.
As an important parameter of laser cleaning, pulse width needs to be controlled reasonably. After reasonably controlling the pulse width, the efficiency control and effect of cleaning will be greatly improved. However, pulse width adjustment will also affect the changes of other parameters, so it is necessary to systematically study the relationship between parameters and a large number of experiments to get the optimal effect.
As an advanced technology in laser manufacturing, laser cleaning machine has great application potential in industrial development. It is of great strategic significance to vigorously develop laser cleaning technology.
Laser Cleaning Machine For Sale
