The working principle and brand of the inverters.
Variable-frequency Drive is a power control device that uses frequency conversion technology and microelectronics technology to control AC motors by changing the motor’s working power supply frequency. Rectification (AC to DC), filtering, inverter (DC to AC), braking unit, drive unit, detection unit micro-processing unit, etc., together constitute the inverter. The frequency converter principle controls the voltage and frequency of the output power supply by adjusting the opening and closing of the internal IGBT and providing the correct power supply voltage according to the motor’s actual needs. Because the frequency converter has a very high-cost performance, and at the same time, can achieve the purpose of energy-saving and speed regulation, it has more and more extensive applications in the industrial automation field.
Many inverters on the market, such as Fuling inverters, Niye inverters, Delta inverters, Aosheng fully sealed inverters, and Flextronics inverters from China. High reputation. Foreign inverters are generally expensive. For CNC cutting machines, the domestically-made frequency inverters have complex production processes, affordable prices, and high quality, sufficient to meet all needs. We recommend Fuling inverters, which have great potential in the cutting machine market competing with each other due to their excellent cost performance, stable torque characteristics, and perfect after-sales guarantee. Filing inverters provide the most stable spindle power guarantee for the cutting machine industry.
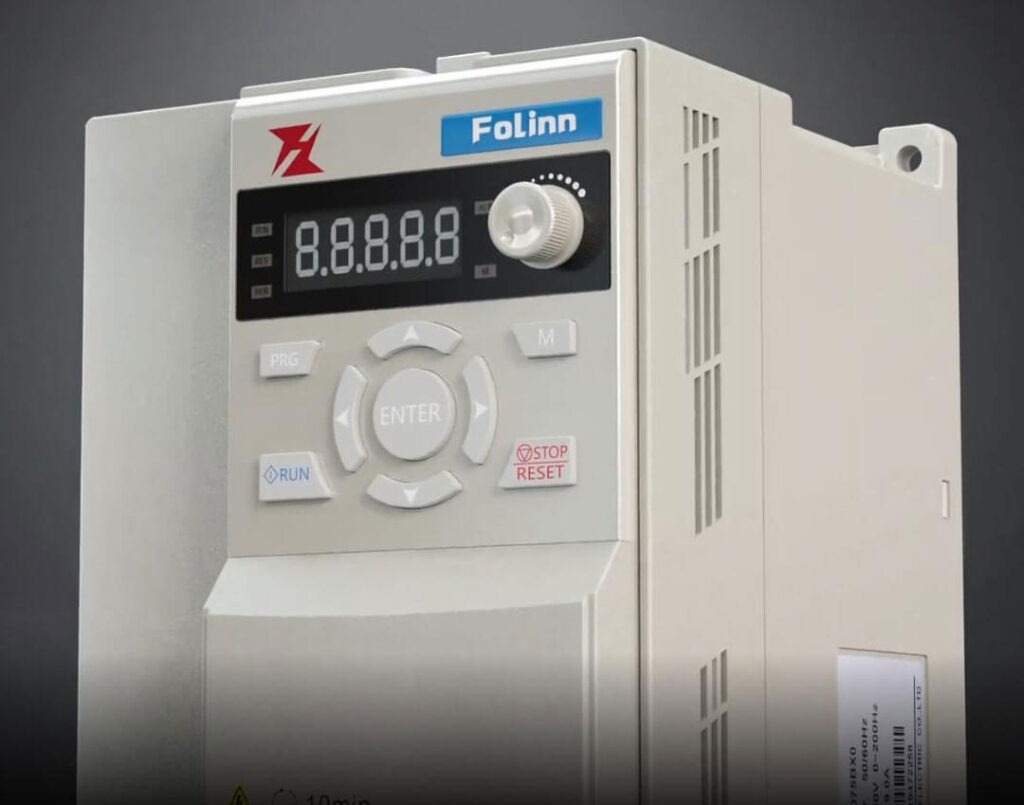
Application of DZB312 Fuling inverters in the machinery industry.
The Fuling Inverter is a brand inverter developed, produced, and sold by Taizhou Fuling Electromechanical Co., Ltd. It is mainly used for variable frequency speed regulation and energy saving of three-phase asynchronous AC motors and used to control and adjust the speed of three-phase AC asynchronous motors. Its production range is wide, including low-voltage Fuling inverter DZB series of conventional products that can achieve 0.55Kw-800KW; high-voltage voltage levels of 3HV, 6HV, 10HV, and the maximum can achieve 40,000KW. Simultaneously, the inverters produced are divided into the H1 series, BD600, and BD330 of general-purpose inverters, the DZB312 and BD337 series industry-specific inverters, the FS series of servo drives, and the KZ series of spindle motors. DZB312 series Fuling inverters for cutting machine with its unique super performance and superior cost performance meets the performance characteristics of spindle requirements such as wide speed range, high-speed stability, strong overload capacity, low-speed torque, short acceleration and deceleration time, etc. , Occupies a larger market share in the domestic cutting machine market.
1. Product features of DZB312 series cutting industry Fuling inverter.
- It can realize the 8-speed operation, which is convenient for Weihong card control.
- Adopt 32-bit microprocessor, sine wave PWM control.
- The scientific algorithm, low interference.
- Adopt independent air duct, suitable for dusty occasions.
- Automatic torque boost and automatic slip compensation function.
- Output frequency range 0~1000.0Hz, up to 2000Hz can be customized.
- Built-in standard 485 communication function.
- Humanized design: factory setting of special macro code parameters for cutting machine, convenient for users to debug.
- Power range: 0.75KW-11KW.
- Factory setting of special macro code parameters for cutting machine, convenient for users to debug.
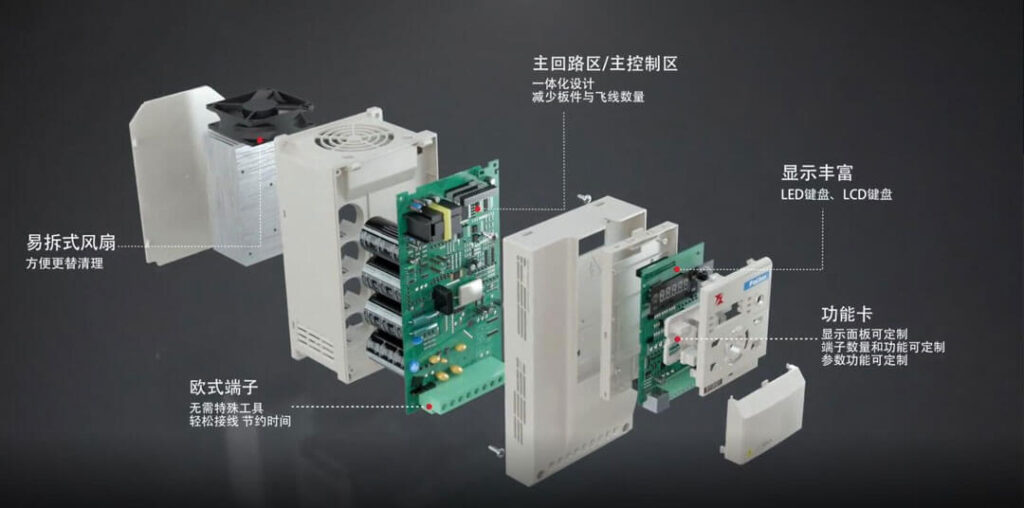
2. How the Fuling inverters work in the cutting machine.
Having said that, I have to introduce the working principle of the CNC cutting machine again. Most of the main drive systems of CNC cutting machine tools use step-less speed change. And the step-less speed change system mainly has two kinds of the DZB series Fuling Inverter spindle system and servo spindle system, generally using DC or AC spindle motor. Drive the main shaft to rotate through the transmission or drive the main shaft to rotate through the transmission belt and the main shaft box’s reduction gear. The spindle box structure is greatly simplified due to the wide speed range of the spindle motor and the step-less speed regulation. The Fuling CNC Router requires the spindle system to adopt infinitely variable speed. At present, the inverter is mostly used to drive the asynchronous AC motor. The spindle motor mostly uses a two-stage high-speed brushless water-cooled motor with low noise and strong cutting force. The running speed is generally 0~24000r/min, and the corresponding inverter running frequency is 0~400Hz. Large cutting machines are equipped with multiple spindle heads to improve processing efficiency, and an Inverter drives multiple spindle motors to work simultaneously.
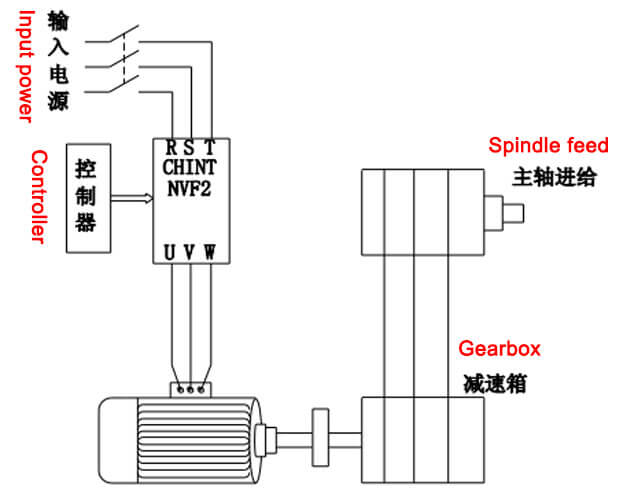
The Fuling inverter’s output frequency is usually 300HZ, some are 400HZ, and even some models can reach a high frequency of 800HZ. And the frequency rating is often based on the factory parameters of the spindle motor. Set the frequency correctly. Make the spindle of the cutting machine play to its best performance. Otherwise, it may reach the risk of damage to the machine. The following two figures are for readers to set the cutting machine inverter as a reference.
The power supply system of the cutting machine has single-phase 220V and three-phase 380V. Most models use a single-phase 220V power supply. The electrical wiring method is divided into two methods according to the different frequency source setting methods. The source of spindle frequency is the analog setting, and the source of spindle frequency is the way of multi-speed setting. The following focuses on the way that the source of spindle frequency is given by analog.
The Fuling inverter accepts the 0~10V analog signal output by the controller, and this voltage value is proportional to the speed control frequency range set by the Fuling inverter parameters. FWD is the forward rotation signal of the inverter. When the controller sends a forward rotation signal, the controller’s output relay will act. The normally open contact of the relay will be closed to provide the signal to the inverter. L1 and L2 are the power input of the inverter. If the inverter chooses three-phase input, connect it to the R, S, and T terminals. TA/TB/TC is the inverter relay output. Usually, the Fuling inverter fault alarm output is selected, and it is connected to the cutting machine controller or external fault indication circuit.
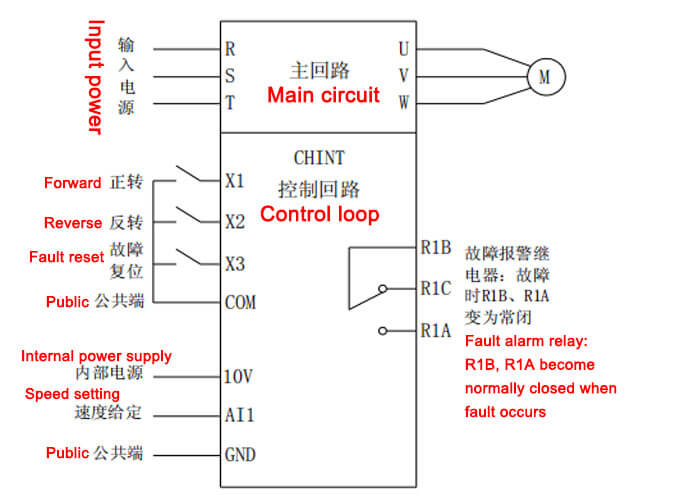
3. Fuling inverter has the following advantages.
CNC cutting machines have been widely used in various industries, especially in advertising production, building decoration, and stone production and processing industries. The Fuling frequency converter on the cutting machine has also solved many problems and facilitated its use.
- Standard frequency output range of 0~600Hz, up to 1500Hz, fully meet the speed regulation range of the cutting machine.
- Two parameter macro functions are added, which can normally run only by adjusting a few parameters, which is convenient for installation and debugging.
- ±20% wide voltage design to meet applications with large voltage fluctuations.
- Dynamic torque current control, fast response to load changes.
- Compact structure, saving installation space.
- Pass strict EMC test, strong anti-interference ability.
- Strict quality management system to ensure stable and reliable operation of products.
Precautions for the use of Fuling inverter
Improper use of the inverter will fail to give full play to its excellent functions and may damage the inverter and its equipment, cause interference, etc. Pay attention to during use:
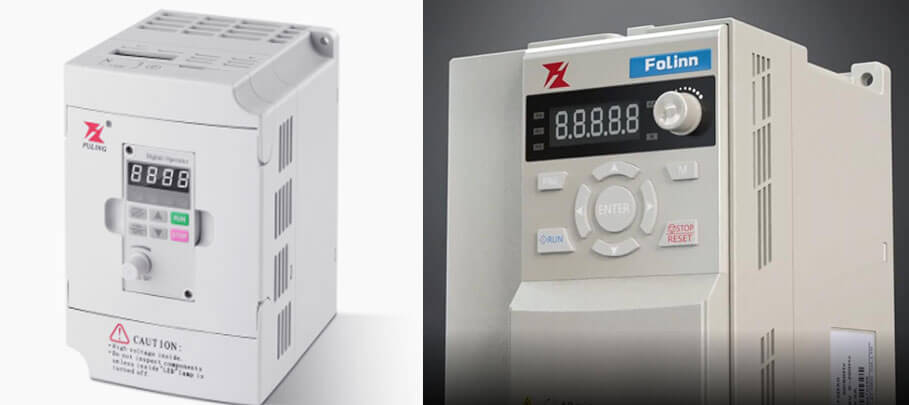
- The Fuling Inverter must be selected by you correctly.
- Read the product Fuling VFD manual carefully, connect, install, and use according to the Fuling inverter DZB 300 user manual’s requirements.
- The inverter device should be grounded reliably to suppress radio frequency interference and prevent electric shock caused by leakage in the inverter.
- The impedance of the power supply line cannot be too small. When the inverter is connected to the low-voltage power grid, when the capacity of the distribution transformer exceeds 500KVA or the capacity of the distribution transformer is greater than 10 times the capacity of the inverter, or when the inverter is connected to a place close to the distribution transformer, the circuit impedance is small, the input is instantaneous A large inrush current to the inverter will damage the rectifier components of the inverter. When the line impedance is relatively small, install an AC reactor between the corresponding transformer and the inverter.
- circuit breakers and contactors cannot directly operate the start and stop of the speed regulation by the Fuling inverter. Still, the control terminals of the frequency converter shall be used for the operation. Otherwise, the inverter will be out of control and may cause severe punishment.
- For the occasion that the inverter drives the ordinary motor for constant torque operation, try to avoid a long-term low-speed operation. Otherwise, the motor’s heat dissipation effect will be poor, and the heat will be serious. If you need to run at low speed and constant torque for a long time, you must use a variable frequency motor.
- When the motor has another brake, the Fuling inverter should work in free stop mode, and the braking action signal should be sent out after the inverter sends a stop command.
- The inverter’s external braking resistor’s resistance value cannot be less than the requirement of the braking resistor allowed by the Fuling inverter. On the premise of meeting the braking requirements, the braking resistance should be larger. Do not short-circuit the terminal that should be connected to the braking resistor. Otherwise, a short-circuit accident may occur through the switch tube during braking.
- When the inverter is connected to the motor, it is not allowed to use a megohmmeter to measure the motor’s insulation resistance. Otherwise, the high voltage output by the megohmmeter will damage the Fuling inverter.
- Correctly handle the problem of speed increase and deceleration. The inverter’s acceleration and deceleration time are too short, and it is easy to be damaged by “electric shock.” Therefore, when the inverter is used, the acceleration and deceleration time should be extended as much as possible if the load equipment allows it.
If the load is heavy, the acceleration and deceleration time should be increased; otherwise, the acceleration and deceleration time can be appropriately reduced;If the load equipment needs to accelerate or decelerate in a short time, you must consider increasing the capacity of the Fuling inverter to avoid too much current that exceeds the rated current of the inverter;If the load equipment requires a short acceleration and deceleration time (for example, within 1s), a brake system should be considered on the Fuling inverter. Generally, larger capacity inverters are equipped with brake systems.
Common faults of Fuling inverter and solutions.
In the daily use of the frequency converter, the most likely occurrence is the fault alarm. To deal with these alarm issues, we must first find the manual and check the alarm code to explain its meaning. Common alarm code functions:
- Under-voltage alarm refers to the input terminal voltage is too low, there may be phase loss, check whether the input side voltage is abnormal
- Over-current, over-voltage, and overload alarm. This generally refers to the power loss after the Fuling inverter has been used for a long time. These types of alarms will appear at this time. The treatment opinion is to reduce the load, the knife does not need to be as deep as before, and at the same time, change the parameters to increase the Fuling inverter’s overcurrent and overload range.
- The module is faulty. This is usually a short circuit or grounding on the output side. At this time, do not forcibly power on the inverter frequently to avoid damage to the inverter. What needs to be done is to check whether the inverter’s UVW three phases are short-circuited and whether the spindle motor plug is connected—fire phenomenon.
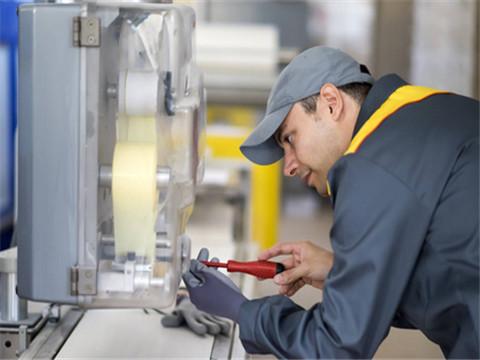
Sometimes the Fuling inverter can’t normally display after power-on. You have to check whether the inverter panel is installed properly, whether the three-phase power enters the inverter’s RST terminal, whether there is fire or smoke, the root cause can be found according to the phenomenon, and the Fuling inverter will be prompted. Don’t power it on for a long time, but frequently power on and power off several times to avoid damage to the switching power supply and capacitor.
In summary, the application of the frequency converter in the CNC cutting machine should not be underestimated. We must be extra careful and take care when selecting and using the Fuling inverter because the frequency converter is used frequently during the machine’s operation, which is very important to the processing quality Effect plays a vital role.