Table of Contents
As an indispensable equipment in modern industrial manufacturing, fiber laser welder‘s stability and reliability are crucial to the continuous operation of the production line. However, any equipment may malfunction during long-term operation. This article will discuss how to provide effective technical support and maintenance services when a fiber laser welder fails to ensure that the equipment quickly returns to normal operation.
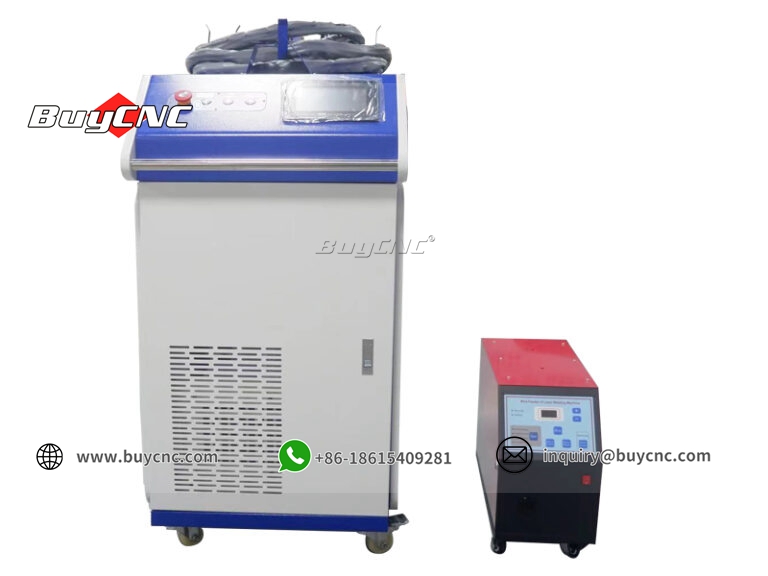
Fiber laser welder technical support service
Troubleshooting and remote support. When a fiber laser welder fails, fault diagnosis needs to be performed first. The technical support team can obtain the operating data and fault phenomena of the equipment through telephone, email or remote login to the system, and conduct preliminary analysis. For problems that can be solved through remote operation, the technical support team will directly provide solutions and remote guidance.
Technical training and documentation support. In order to improve users’ ability to operate and maintain fiber laser welders, the technical support team should provide comprehensive technical training and documentation support. The training content should include equipment operating specifications, daily maintenance and maintenance methods, common faults and treatment methods, etc. At the same time, detailed equipment manuals, operating guides and technical reference documents should be provided for users to consult at any time.
Upgrade and improvement suggestions. The technical support team should pay attention to the technological development of fiber laser welders and keep abreast of the latest technology and equipment improvements in the industry. Based on the actual needs of users and equipment operation conditions, upgrade and improvement suggestions are provided to help users improve equipment performance and stability.
Fiber laser welder maintenance services
Quick response and on-site repair. Once it is determined that the fiber laser welder needs on-site maintenance, the maintenance service team should respond quickly and arrange for professional maintenance personnel to go to the site. Maintenance personnel should carry the necessary tools and spare parts to perform troubleshooting and repairs on site. For problems that cannot be solved on site, we should communicate with the user in a timely manner and arrange to return to the factory for repair or replacement of the equipment.
Maintenance reports and feedback. After the maintenance is completed, the maintenance personnel should prepare a detailed maintenance report to record the fault phenomenon, cause of the fault, maintenance process and results and other information. At the same time, the maintenance report should be fed back to the user and the technical support team in a timely manner so that the user can understand and supervise the maintenance status of the equipment.
Maintenance quality assurance. To ensure maintenance quality, the maintenance service team should establish a strict quality management system and monitor the entire maintenance process. For replacement spare parts, ensure that their quality meets relevant standards and requirements. At the same time, the repair results should be accepted and tested to ensure that the equipment returns to normal operation.
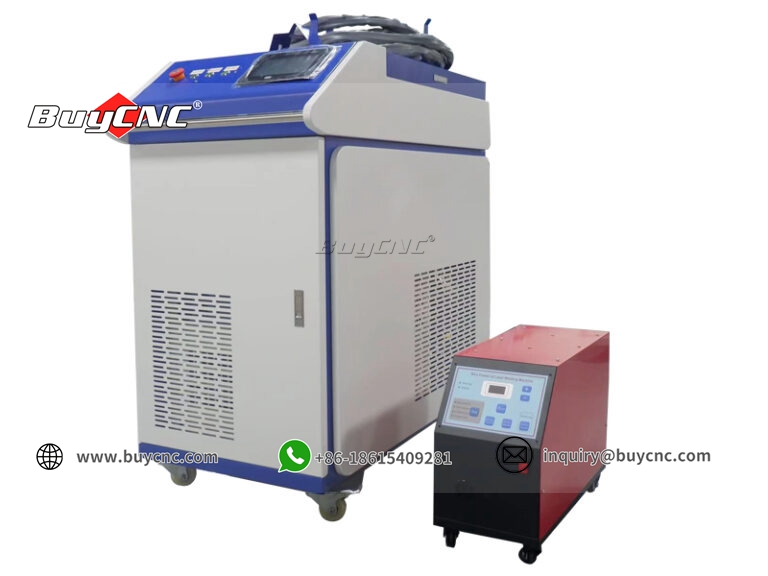
When a fiber laser welder fails, providing effective technical support and maintenance services is the key to ensuring that the equipment quickly returns to normal operation. By providing technical support services such as fault diagnosis and remote support, technical training and documentation support, upgrade and improvement suggestions, as well as maintenance service measures such as rapid response and on-site maintenance, maintenance reports and feedback, and maintenance quality assurance, we can ensure that the fiber laser welder fails when it fails. receive timely and effective processing and support. At the same time, by continuously improving service processes and strengthening customer relationship management, user satisfaction and loyalty can be improved, laying a solid foundation for the long-term development of the enterprise.