What does feed rate mean?
In CNC router machine parts processing, the feed speed Vf refers to the relative movement speed between the tool and the workpiece along the cutting feed direction. That is, the speed at which the surface to be processed is continuously inputted to the cutting. The feed rate is directly related to the cutting force overcome by the router machine. The feed rate not only affects the surface roughness and accuracy of the machined parts but is also closely related to the service life and production efficiency of the tool and router machine. Therefore, better control of the feed speed is essential for machining parts and engraving machinery. In the process of cutting parts of different materials, it is first necessary to refer to the router machine’s technical parameters and the requirements of part roughness and precision, and then select a reasonable range of feed speed adjustment to meet the requirements of the processing technology. The feed rate value in actual machining is adjusted by the numerical control machining feed rate cutting speed value F code. The feed rate overrides switch on the machine operation panel. The numerical control system completes the position control interpolation calculation according to the determined speed value. It outputs the pulse frequency source corresponding to the speed to drive the servo control device.
The choice of cutting tools and cutting parameters is one of the main technical issues of the CNC machine. Choose different tools for different processing materials. The most critical factor of machining quality is the reasonable choice of cutting parameters. Cutting parameters are the basic control quantities of the CNC machine. Among them, the feed speed V f greatly influences the quality of CNC machine workpieces. If the feed speed is not properly selected, it is not only difficult to ensure the machining accuracy of the workpiece, and it is difficult to control the machining cost, but also may cause damage to the router machine due to excessive cutting force.
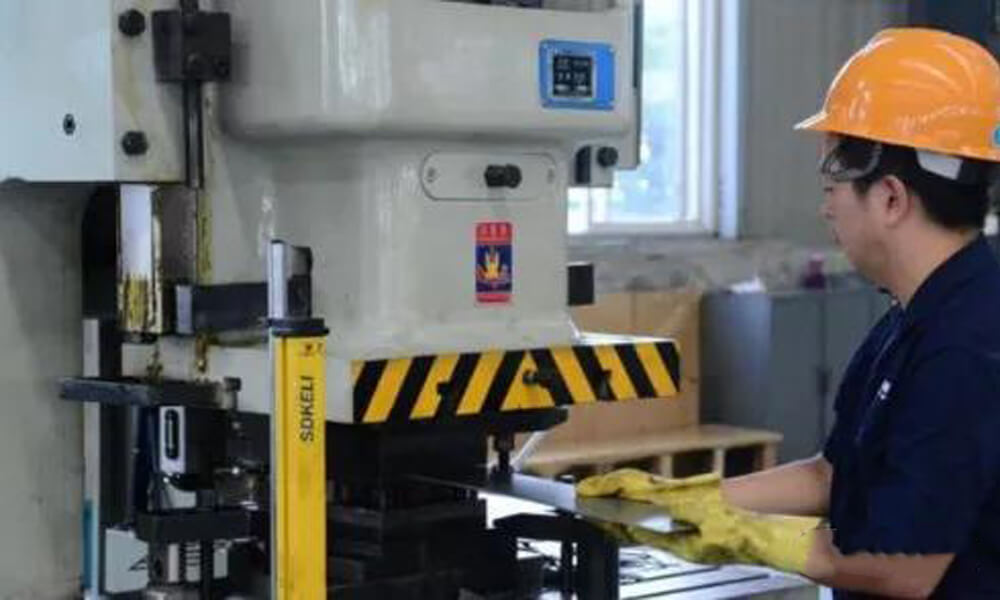
What is the principle of CNC machine feed rate?
1. Feed speed command method.
According to the ISO code instruction standard of CNC router machines, there are two instruction methods for setting the processing program’s feed rate, namely G94 and G95.
The G94 command specifies the tool feed per minute (unit: mm/min), and the G95 command specifies the tool feed per revolution of the CNC machine spindle (unit: mm/r). To better understand these two methods, for example, the CNC machine program segment G94G01X10Y20F100, the program’s feed rate is 100 mm/min; the CNC machine program segment G95G01X10Z5F0.3, the feed rate of the tool programmed in the program is 0.3 mm/r.
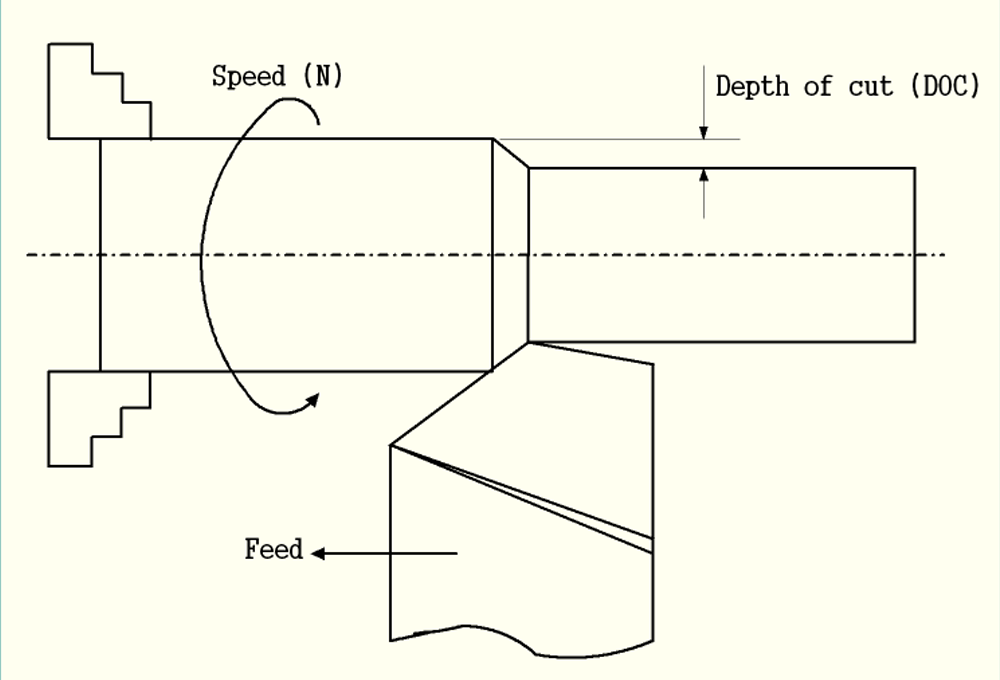
2. What is the relationship between cutting speed, cutting tool, and feed speed?
After reading this, to better understand the cutting speed of the CNC machine, this article will introduce the relationship between the cutting speed, the amount of cutter and the feed speed.
(1)Selection criteria for cutting the amount
When roughing, generally improve the yield rate, but also consider the economy and processing cost. When semi-finishing and finishing, the cutting power, economy and processing cost should be taken into consideration on the premise of ensuring the processing quality. The detailed value should be determined according to the router machine manual, cutting parameter manual, and experience.
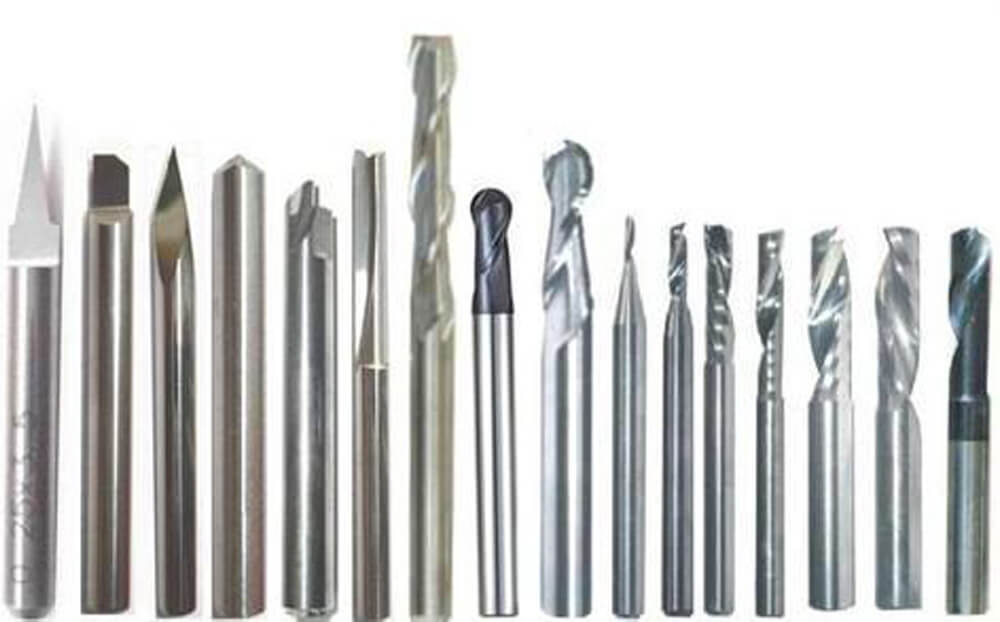
Starting from the tool’s durability, the order of selection of the cutting amount is: first confirm the amount of the back tool, secondly confirm the feed amount, and finally confirm the cutting speed.
(2)Confirmation of the amount of knife.
The amount of back feed is determined by the rigidity of the router machine, workpiece and tool. Under the condition of a certain rigidity, the amount of back-grabbing should be equal to the machining allowance of the workpiece as much as possible, to reduce the number of passes and increase the output power.
Criteria for confirming the amount of back knife:
①When the surface roughness value of the workpiece is required to be Ra12.5μm~25μm if the machining allowance of the CNC machine is less than 5mm~6mm, the rough machining can meet the requirement with one feed. However, when the margin is large, the processing system’s rigidity is poor, or the router machine power is lacking, the feed can be completed multiple times.
②When the workpiece’s surface roughness value is required to be Ra3.2μm~12.5μm, and it can be divided into two steps: rough machining and semi-finish machining. The amount of back-cutting during rough machining is the same as before. Leave 0.5mm~1.0mm margin after rough machining and cut off during semi-finish machining.
③When the workpiece’s surface roughness value is required to be Ra0.8μm~3.2μm, and it can be divided into three steps: rough machining, semi-finishing, and finishing. For semi-finish machining, the amount of the back knife is 1.5mm~2mm. When finishing, the amount of the back knife is 0.3mm~0.5mm.
(3)Confirmation of feed.
The feed amount is mainly based on the machining accuracy and surface roughness of the parts. Simultaneously, the material selection of the tool and the workpiece also has a great influence. The maximum feed rate is limited by the rigidity of the router machine and the function Criteria for confirming the feed rate:
①When the workpiece’s quality requirements can be ensured, to increase the output power, a higher feed speed can be selected. Generally selected in the range of 100~200m/min.
②When cutting, processing deep holes or processing with high-speed steel tools, a lower feed rate should be selected, generally within the range of 20-50m/min.
③When the machining accuracy and surface roughness are required to be high, the feed speed should be lower, generally within the range of 20-50m/min.
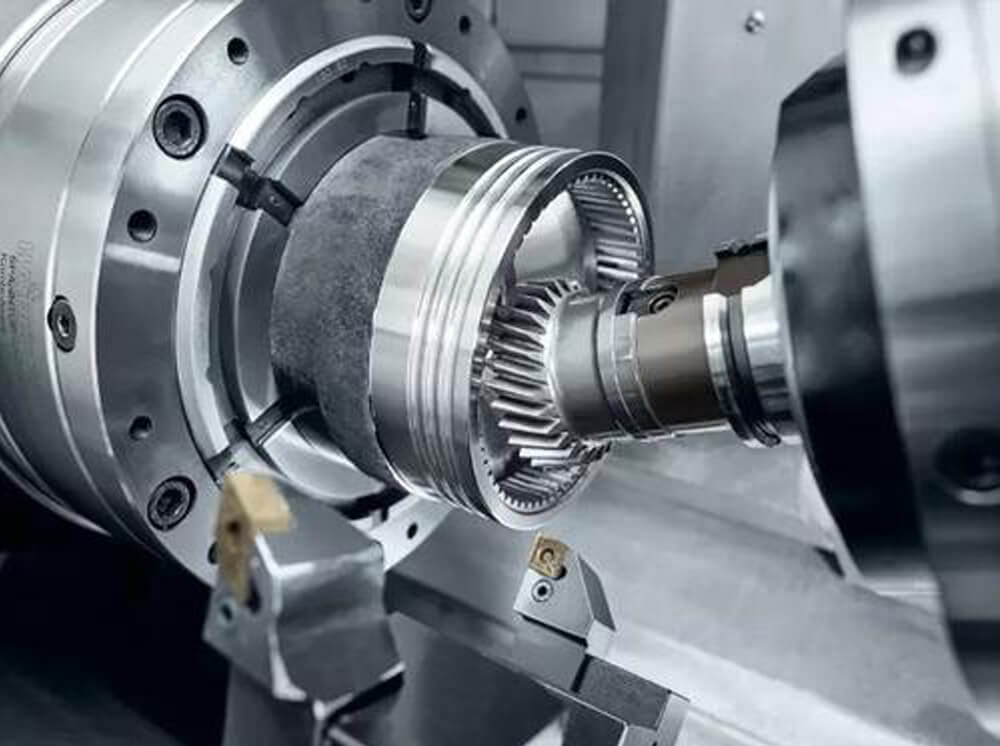
④When the tool is idle, especially when it is “zero return” at a long distance, the highest feed rate set by the CNC system of the router machine can be selected of the feed system.
(4)Confirmation of spindle speed.
The spindle speed should be selected according to the permitted cutting speed and the workpiece’s diameter (or tool). The calculation formula is:
n=1000v/πD
v—-cutting speed, in m/min, determined by the durability of the tool;
n—-spindle speed, the unit is r/min;
D—-workpiece diameter or tool diameter, in mm.
The calculated spindle speed n should ultimately be selected according to the router machine manual, some or close to the router machine.
In short, the detailed numerical value of cutting parameters should be confirmed by analogy based on the function of the router machine, related manuals and combined with practical experience. At the same time, the spindle speed, cutting depth and feed speed can be used to each other to form the best cutting amount.
3. What are the factors that affect the feed rate?
According to the cutting process and machining quality feedback during the CNC machine process, the actual feed speed is adjusted through the feed rate override switch on the machine operation panel. Therefore, the feed axis’s actual feed speed is obtained by program conversion of the CNC system according to the override value corresponding to the override switch and the F value set in the CNC machine program.
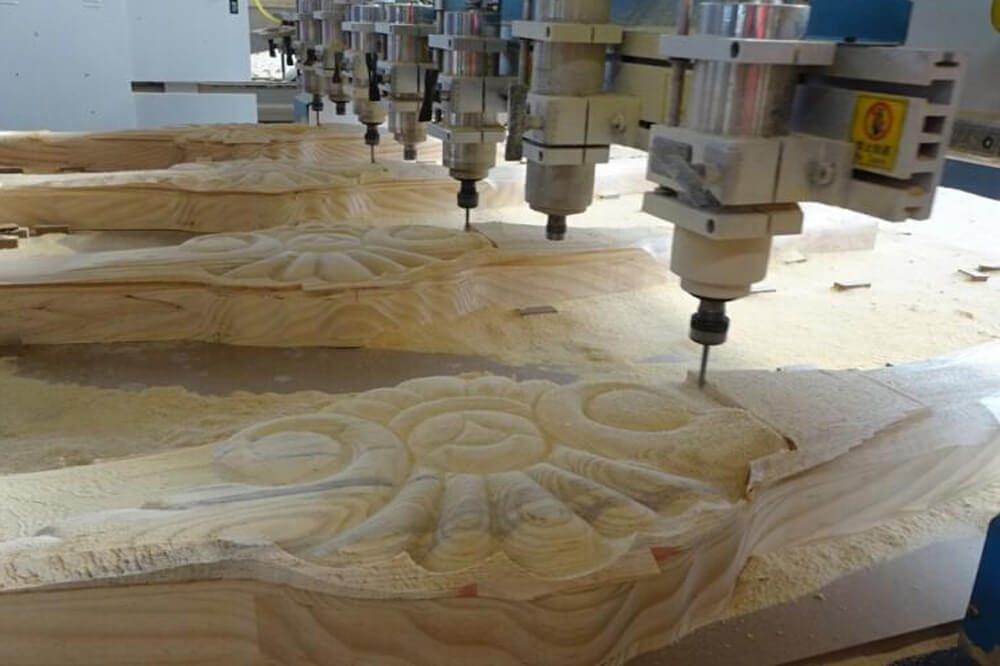
4. How the CNC system adjusts the feed rate?
The CNC system adjusts the feed speed, scans the override switch’s status position according to the PLC program, and obtains the override value through the PLC program coding instruction calculation. The result of the multiplying factor value and the F value is transmitted to the interpolation operation controller for interpolation operation, thereby controlling the actual running speed of the feed axis. When the numerical control system controls the movement of each coordinate axis through interpolation operation, it also automatically controls the feed movement speed of the router machine through the interpolation operation preprocessing program to ensure that the router machine does not produce shock, desynchronization, or overshoot during start and stop—process or oscillation, etc.
Under the premise of ensuring processing quality, selecting the maximum safe feed rate to make full use of CNC router machines’ potential and improve production efficiency is the main purpose of feed rate optimization and servo adjustment in high-speed and high-precision machining.
How to optimize the feed rate of processing mild steel parts?
With the rapid development of science and technology, mechanical parts’ manufacturing precision and complexity are also becoming higher and higher, especially in aerospace, cutting-edge military, precision instruments, etc. The traditional processing technology is difficult to adapt to modern manufacturing Industry needs. Therefore, CNC router machines are widely used as a kind of innovative technical equipment. The numerical control technology is the basis for the modern industry to realize automation, flexibility, and integrated production. It is a modern manufacturing technology with intensive knowledge and capital. The milling parameters of the CNC milling machine mainly include milling speed, feed (including feed speed and feed per tooth, etc.), side cutter (milling width) and back cutter (milling depth). These four elements are the most fundamental factors in milling processing, and they are also the basic control quantities in CNC milling processing. The choice of milling parameters, especially the choice of feed speed, has always troubled many technicians. Different machining materials need to choose different tools, and the most critical factor of machining quality is the reasonable choice of cutting parameters.
The feed speed has a great influence on the surface quality of the CNC machined workpiece. For example, at a given speed, the higher the feed rate, the surface roughness of the processed parts will also increase, and it also has an impact on other parameters, such as processing costs. This article comprehensively researches various factors to determine the optimal feed rate. Low-carbon steel is a widespread material. Its hardness is roughly in the range of 179 to 229HBS, and the hardness value is low. The requirements on the tool need not be too high, and it is easy to process. Simultaneously, it has the advantages of low price, so we choose low carbon steel as the processing material to study the optimization of feed speed. Giving the optimized value under different speed conditions ensures the actual production will produce certain help and guidance.
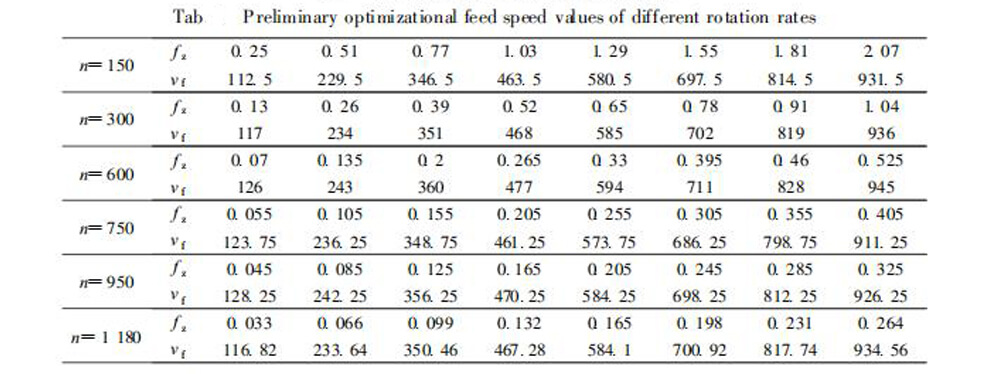
The data found that at a given speed, the greater the feed rate, the greater the feed rate, the smaller the processing person-hours and the processing cost and the overall evaluation value of the two, but the greater the surface roughness. Simultaneously, the processing working hours, processing costs, and comprehensive evaluation values are all negatively related to the feed per tooth f z (equivalent to the feed speed v f). The roughness of the machined surface is positively correlated with FZ. It can be seen that when the feed per tooth is given, the higher the speed, the greater the feed speed. The lower the processing cost, comprehensive evaluation value and roughness value. That is, when the feed per tooth is the same, the feed speed is positively related to the speed n (which can be equivalent to the milling speed VC); while the processing person-hours, processing costs, and comprehensive The evaluation values are all negatively related to the speed n. Therefore, in the actual production process, the speed n (which can be equivalent to the milling speed v c) should be as large as possible within the allowable range.
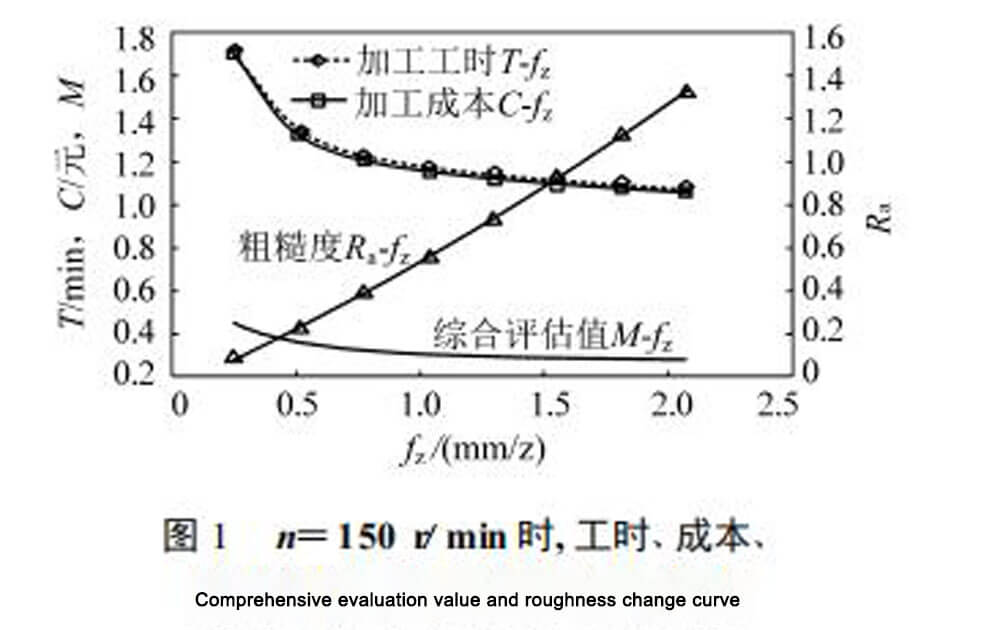